2025 Autor: Howard Calhoun | [email protected]. Naposledy změněno: 2025-06-01 07:13
Ve zpracovatelském průmyslu a stavebnictví je nedestruktivní testování jednou z nejoblíbenějších metod diagnostiky materiálů. Pomocí této metody stavitelé hodnotí kvalitu svarových spojů, kontrolují hustotu v určitých úsecích konstrukcí a odhalují hluboké defekty a kazy. Diagnostické magnetické defektoskopy mohou detekovat povrchové i podpovrchové poškození s vysokou přesností.
Zařízení zařízení
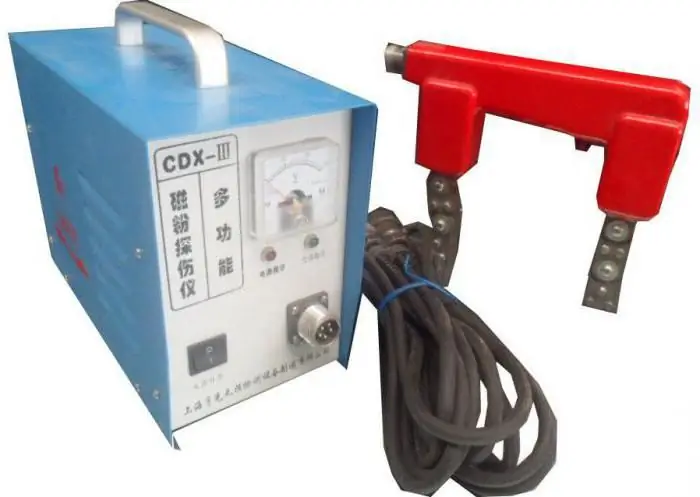
Základem segmentu magnetických tloušťkoměrů a defektoskopů jsou ruční přístroje opatřené magnetizovatelnými pracovními tělísky - obvykle ve formě kleští. Navenek se jedná o malá zařízení, jejichž náplní je elektromagnet, který reguluje póly působení vln. Střední třída umožňuje pracovat s magnetickou permeabilitou, jejíž koeficient je vyšší než 40. Tělo je opatřeno ergonomickou rukojetí, díky které lze přístroj používat i na těžko dostupných místech. Pro napájení elektrickým proudem jsou přístroje vybaveny také kabelem připojeným buď ke generátorové stanici (pokud se pracuje venku) nebo k domácí elektrické síti 220 V. Sofistikovanější zařízení pro nedestruktivní testovánímá stacionární základnu připojenou k počítači. Takové diagnostické nástroje se častěji používají pro kontrolu kvality vyráběných dílů ve výrobě. Provádějí kontrolu kvality a opravují nejmenší odchylky od standardních ukazatelů.
Ferosondové defektoskopy
Různá magnetická zařízení určená k detekci defektů v hloubce až 10 mm. Zejména se používají k opravě nespojitostí ve struktuře konstrukcí a dílů. Mohou to být západy slunce, mušle, praskliny a vlasové linie. Metoda fluxgate se také používá k posouzení kvality svarů. Po skončení pracovního sezení mohou magnetické defektoskopy tohoto typu v rámci komplexní diagnostiky určit i úroveň demagnetizace dílu. Z hlediska aplikace na díly různých tvarů a velikostí nemají zařízení prakticky žádná omezení. Ale opět bychom neměli zapomínat na maximální hloubku analýzy struktury.
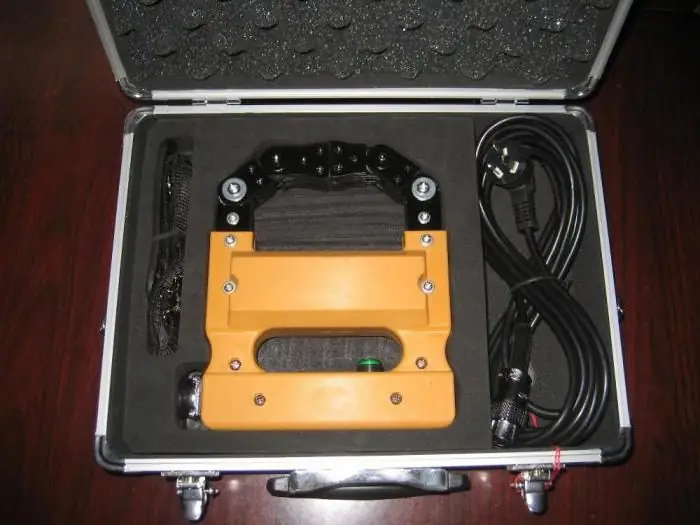
Magnitografické defektoskopy a detektory vířivých proudů
Pomocí magnetografických zařízení může operátor detekovat vady produktu v hloubce 1 až 18 mm. A opět, cílovými znaky odchylek ve struktuře jsou nespojitosti a vady svarových spojů. Mezi vlastnosti techniky testování vířivými proudy patří analýza interakce elektromagnetického pole s vlnami generovanými vířivými proudy, které jsou přiváděny do předmětu řízení. Nejčastěji se defektoskop na bázi vířivých proudů používá ke zkoumání výrobků vyrobených z elektricky vodivých materiálů. Zařízení tohoto typuvykazují vysoce přesný výsledek při analýze dílů s aktivními elektrofyzikálními vlastnostmi, ale je důležité vzít v úvahu, že pracují v malé hloubce - ne více než 2 mm. Pokud jde o povahu defektů, metoda vířivých proudů umožňuje odhalit nespojitosti a trhliny.
Detektory defektů magnetických částic
Taková zařízení jsou také zaměřena především na povrchové vady, které lze opravit v hloubce až 1,5-2 mm. Zároveň je umožněna možnost výzkumu odhalit širokou škálu vad - od parametrů svaru až po detekci známek delaminace a mikrotrhlin. Princip činnosti takového nedestruktivního testovacího zařízení je založen na aktivitě práškových částic. Působením elektrického proudu jsou směrovány k nehomogenitě magnetických kmitů. To vám umožní opravit nedokonalosti povrchu cílového předmětu studia.
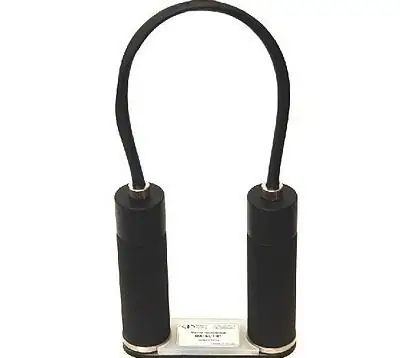
Nejvyšší přesnost při určování vadných oblastí touto metodou bude přítomna, pokud rovina vadné oblasti svírá se směrem magnetického toku úhel 90 stupňů. S vychýlením z tohoto úhlu klesá i citlivost nástroje. V procesu práce s takovými zařízeními se také používají další nástroje k opravě parametrů defektů. Například magnetický defektoskop "Magest 01" je v základní konfiguraci vybaven dvojitou lupou a ultrafialovou svítilnou. To znamená, že přímé určení vady na povrchu provádí operátor vizuální kontrolou.
Příprava na práci
Přípravné aktivity lze rozdělit do dvou skupin. První bude zahrnovat přímou přípravu pracovní plochy a druhá - nastavení zařízení. Pokud jde o první díl, díl musí být očištěn od rzi, různých druhů mastnoty, olejových skvrn, nečistot a prachu. Vysoce kvalitní výsledek lze získat pouze na čistém a suchém povrchu. Dále se nastaví defektoskop, ve kterém bude klíčovým krokem kalibrace s ověřením podle standardů. Posledně jmenované jsou vzorky materiálů s vadami, které lze použít k vyhodnocení správnosti výsledků analýzy zařízení. V závislosti na modelu můžete také nastavit rozsah pracovní hloubky a citlivost. Tyto indikátory závisí na úkolech zjišťování vad, vlastnostech zkoumaného materiálu a schopnostech samotného zařízení. Moderní high-tech defektoskopy také umožňují automatické nastavení podle zadaných parametrů.
Magnetizace dílu
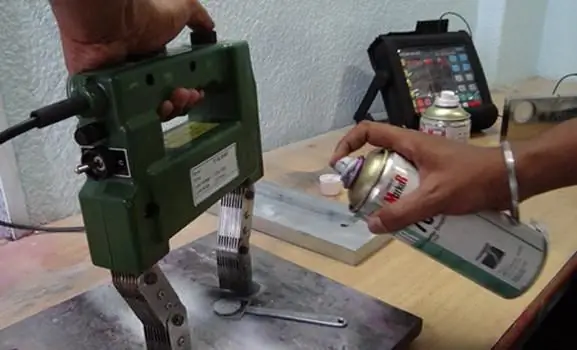
První fáze pracovních operací, při kterých se provádí magnetizace zkoumaného předmětu. Zpočátku je důležité správně určit směr proudění a typ magnetizace s parametry citlivosti. Například prášková metoda umožňuje provádět pólový, kruhový a kombinovaný dopad na součást. Zejména kruhová magnetizace se provádí průchodem elektrického proudu přímo výrobkem, hlavním vodičem, vinutím nebo samostatnou sekcí prvku s připojením elektrických stykačů. VV režimu pólové akce zajišťují magnetické defektoskopy magnetizaci pomocí cívek, v médiu elektromagnetu, pomocí přenosného elektromagnetu nebo pomocí permanentních magnetů. V souladu s tím vám kombinovaná metoda umožňuje kombinovat dvě metody připojením dalšího zařízení v procesu magnetizace obrobku.
Použití magnetického indikátoru
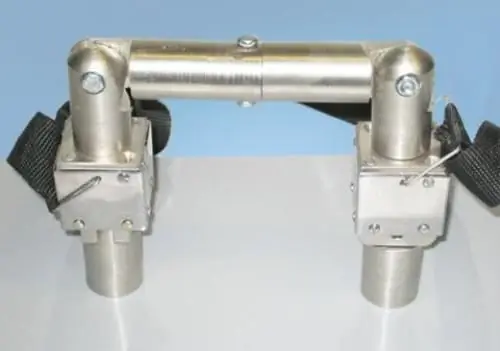
Materiál indikátoru se aplikuje na předem připravený a zmagnetizovaný povrch. Umožňuje vám identifikovat chyby součásti pod vlivem elektromagnetického pole. Již bylo řečeno, že v této kapacitě lze použít prášky, ale některé modely také pracují se suspenzemi. V obou případech je před prací důležité zvážit optimální podmínky pro používání zařízení. Například magnetický defektoskop "MD-6" se doporučuje používat při teplotách od -40 do 50 °C a při vlhkosti vzduchu do 98%. Pokud podmínky splňují požadavky na provoz, můžete začít s aplikací indikátoru. Pudr se nanáší celoplošně - takže je zajištěno i malé pokrytí oblastí, které nejsou určeny ke studiu. To poskytne přesnější obraz vady. Suspenze se aplikuje proudem pomocí hadice nebo aerosolu. Existují také způsoby ponoření dílu do nádoby s magnetickou indikátorovou směsí. Poté můžete přejít přímo k odstraňování problémů s produktem.
Kontrola dílu
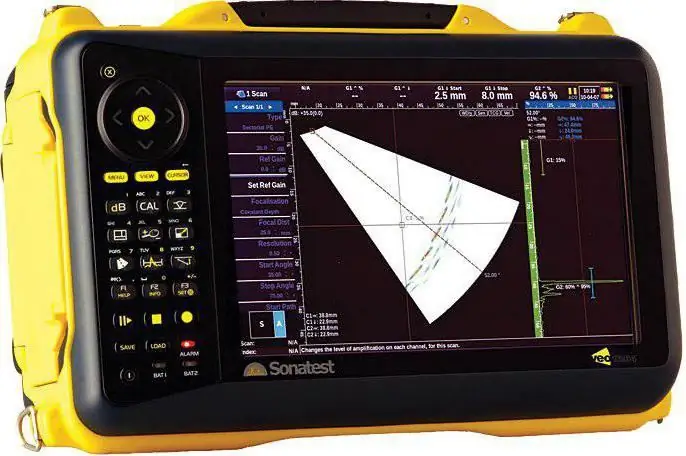
Operátor musí počkat, dokud neskončí činnost indikátoru,ať už jde o částice prášku nebo suspenzi. Výrobek je vizuálně kontrolován výše uvedenými zařízeními ve formě optických zařízení. V tomto případě by zvětšení těchto zařízení nemělo překročit x10. V závislosti na požadavcích na vyšetření může operátor také pořizovat snímky pro přesnější počítačovou analýzu. Multifunkční magnetické defektoskopy-stanice mají v základní výbavě vybavení pro dekódování replik s usazeninami prášku. Výkresy získané v průběhu třídění jsou následně porovnány se standardními vzorky, což nám umožňuje učinit závěr o kvalitě produktu a jeho přípustnosti pro zamýšlené použití.
Závěr
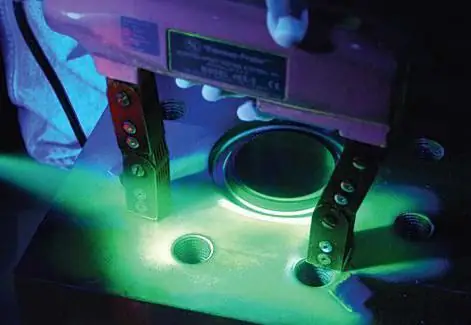
Přístroje pro detekci magnetických vad jsou široce používány v různých oblastech. Mají ale i nevýhody, které omezují jejich použití. V závislosti na provozních podmínkách k nim patří požadavky na teplotní podmínky a v některých případech nedostatečná přesnost. Jako univerzální prostředek kontroly odborníci doporučují používat vícekanálový magnetický defektoskop, který je schopen podporovat i funkci ultrazvukové analýzy. Počet kanálů může dosáhnout 32. To znamená, že zařízení bude schopno udržovat optimální parametry detekce chyb pro stejný počet různorodých úkolů. Kanály jsou v podstatě chápány jako počet provozních režimů zaměřených na určité vlastnosti cílového materiálu a podmínky prostředí. Takové modely nejsou levné, ale poskytujísprávnost výsledků při zjišťování povrchových vad a vnitřní struktury různého druhu.
Doporučuje:
Nastavitelný ventil - typy ovládání a konstrukční prvky
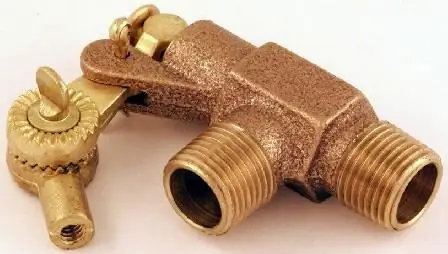
Pokud je v domovním potrubí regulovatelný ventil ovládán ručně, pak se v průmyslovém provozu používají různé typy pohonů. Na armaturách jsou připevněna čidla, která snímají indikátory stavu přepravovaného produktu
Větrání průmyslových prostor: typy, požadavky, design a ovládání
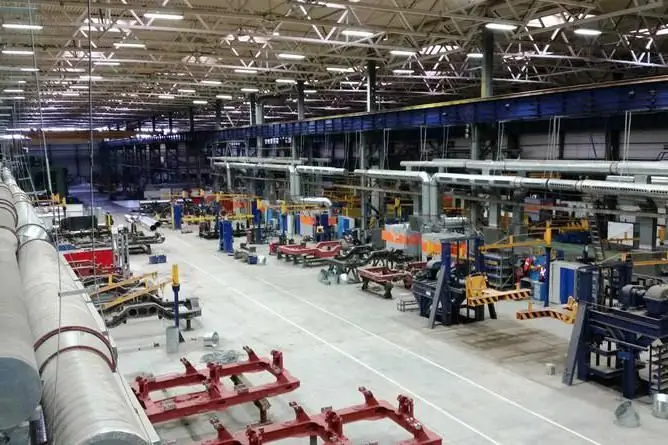
Navrhování ventilace průmyslových prostor je poměrně obtížný úkol. Vytváření schémat se provádí s ohledem na specifika podniku. Hlavním úkolem ventilačního systému průmyslových prostor je rychle „zachytit“všechny nečistoty a odstranit je
Izolační ventily – co to je? Zařízení, aplikace
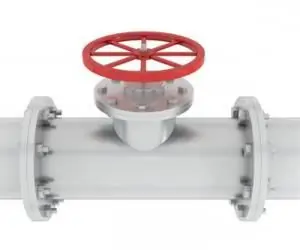
Pojem „uzavírací ventily“označuje zařízení, která řídí sílu průtoku určitého média. Nejčastěji jsou na potrubí přítomny prvky ventilů. Dále pochopíme, na jaké typy ventilů se dělí, co to je a kde se používá
Válce "Rockwool" (Rockwool): popis, zařízení, princip činnosti, aplikace, fotografie
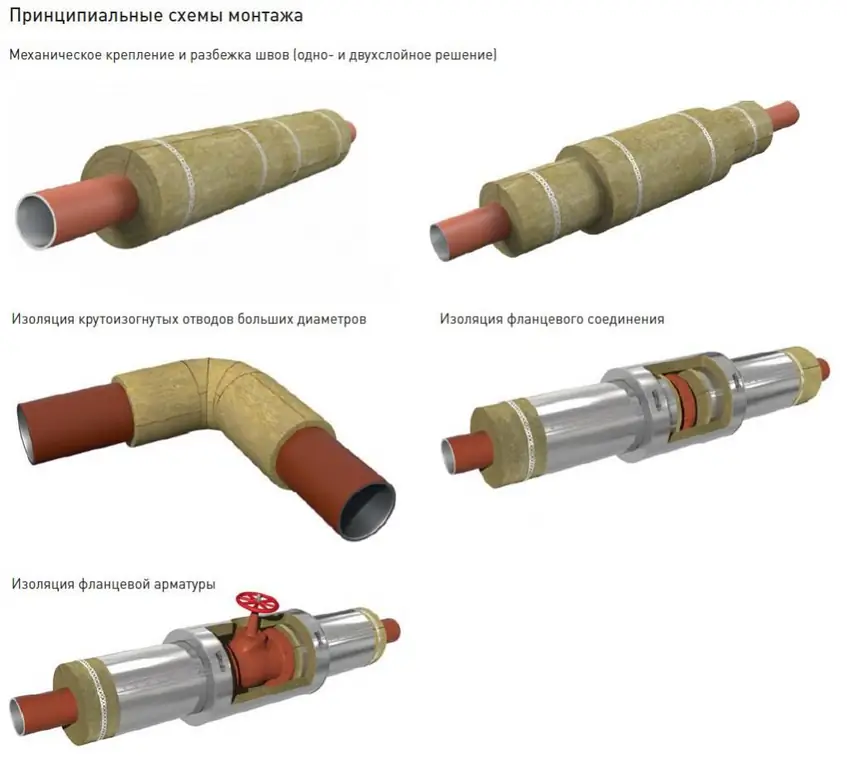
Životnost trubek se snižuje v důsledku jejich použití v podmínkách nízkých teplot a vysoké vlhkosti. Tento problém lze však vyřešit použitím moderních ochranných materiálů z minerální vlny. Mezi obrovskou rozmanitostí návrhů na trhu nejsou válce Rockwool poslední. Společnost zahájila svou činnost před více než stoletím v Dánsku. Za dobu své existence dosáhla spotřebitelského uznání
Automatizace je věda o ovládání bez lidského zásahu
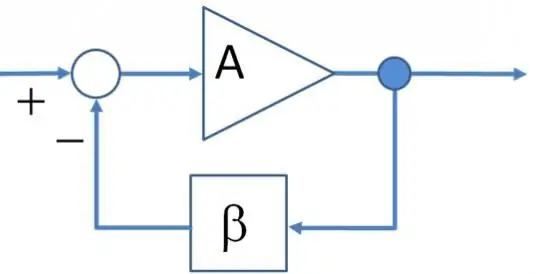
Zařízením, bez kterého není automatizace možná, je regulátor. Může být extrémně jednoduchý (dvoupolohový), jako například v žehličce, nebo složitý, představující elektronickou jednotku, která poskytuje speciální algoritmus