2025 Autor: Howard Calhoun | [email protected]. Naposledy změněno: 2025-06-01 07:13
Odlévání do skořepinových forem se také nazývá skořepinové lití. A v zahraničí se tento způsob práce nazývá Shell.
Obecné informace
V dnešním průmyslovém průmyslu se používá mnoho různých metod odlévání. Kromě skořepinového lití se používá také lití na vytavitelný model, do kovových forem a několik dalších metod. Celková výhoda těchto metod odlévání ve srovnání s litím do písku spočívá v tom, že výsledkem jsou přesnější koncové materiály, pokud jde o tvar i rozměry. Kromě toho se snižuje počet nerovností na povrchu takových výrobků. Ve vzácnějších případech se ale přesto stává, že odpadá nutnost následného obrábění po tavení. Ke všemu navíc přispívá využití odlévání do skořepinových forem a další metody k tomu, že tento proces lze co nejvíce mechanizovat, v důsledku čehož se zvyšuje i jeho automatizace. A to samozřejmě výrazně zvyšuje produktivitu jakéhokoli průmyslového zařízení.
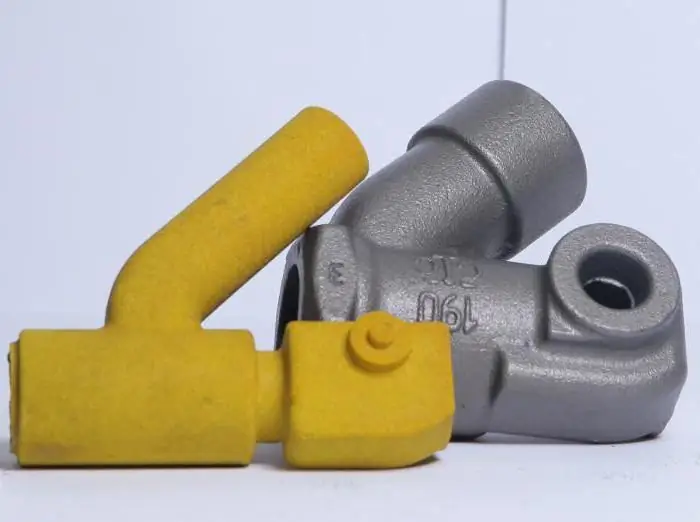
Odlévání mušle
Pokud o tom mluvíme konkrétněTato metoda byla poprvé představena v továrnách již v roce 1953. V současné době je metoda používána poměrně široce. Právě odlévání do skořepinových forem například vyrábí většinu dílů pro traktor Kirovets. Všechny díly, které jsou vyráběny touto metodou, jsou nejvyšší kvality z oceli nebo litiny. Skořápkové odlévání je metoda, při které má konečný výsledek odlévání tvar sestávající ze dvou pískopryskyřičných skořepin. Také tento způsob výroby dílů se používá pouze v případech, kdy je potřeba vytvořit díl s malými nebo středními rozměry, ale zároveň s vysokou přesností. Příklady aplikací pro tuto metodu odlévání jsou díly motoru nebo tenkostěnné odlitky.
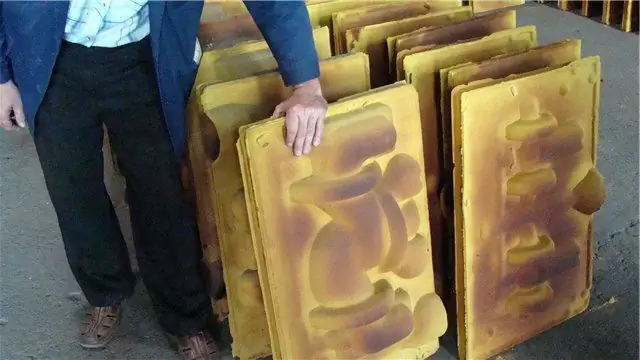
Esence of the Way
Touto pracovní metodou můžete získat různé díly pro ventilátory, motory, čerpadla nebo textilní stroje. Maximální délka přijatého produktu však nesmí přesáhnout 1 metr a nesmí být těžší než 200 kg.
Podstata lití do skořepinových forem je založena na určitých vlastnostech termosetových pryskyřic, které jsou součástí směsí písku a pryskyřice. Výhodou použití takových komponent je, že tyto pryskyřice mají tendenci rychle a trvale tvrdnout, když jsou ošetřeny teplotou 200-250 stupňů Celsia.
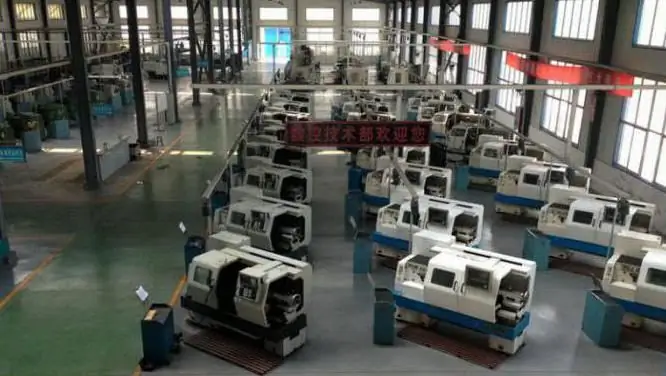
Výroba skořepinové formy pro odlévání
Pro výrobu formy pro následné odlévání je potřeba mít jemnozrnný křemičitý písek, který je dodáván s přídavkem termosetové pryskyřice, která je jejím spojovacím prvkem pro získání plnohodnotné skořepinové formy. Tyto materiály, zejména pryskyřice, jsou zvoleny proto, že tvrdnou, když projdou určitou teplotní bariérou. Výrobní proces je následující. Nejprve se pryskyřice zahřeje na 140-160 stupňů Celsia. Vlivem takového prostředí se promění v tekutou adhezivní hmotu, která zcela obalí formu z křemenného písku.
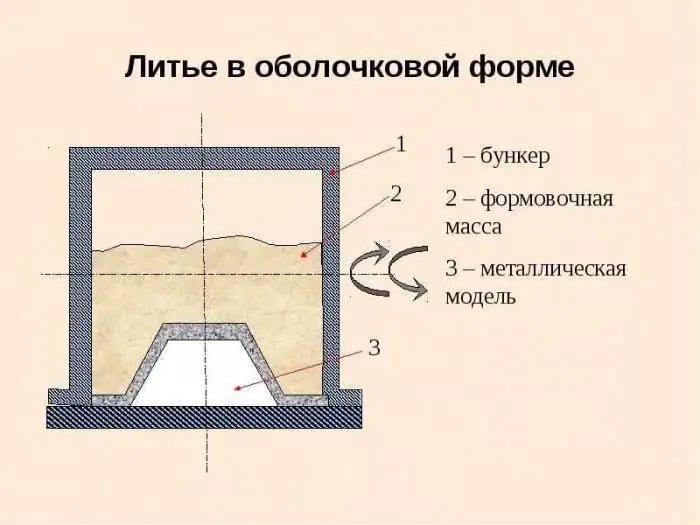
Rozsah odlévání do skořepinových forem je poměrně široký, a proto je proces výroby forem převeden na automatiku nebo automatizaci.
Po úplném pokrytí formy pryskyřicí se teplota zvýší na 200-250 stupňů Celsia. Tento teplotní práh stačí k tomu, aby lepicí hmota nevratně ztvrdla a vytvořila tvar. Dále, když začíná proces odlévání dílů, to znamená, když roztavený kov vstupuje do formy, teplota v ní dosahuje asi 600 stupňů. Tento režim stačí k tomu, aby se pryskyřice neroztavila, ale vyhořela, přičemž na samotné formě zůstanou póry, což usnadňuje únik plynů.
Výhody a nevýhody lití do skořepinových forem
Jako každý jiný výrobní proces má i tento svá pro a proti. Srovnáme-li tento způsob odlévání např. s odlévánímběžné pískové formy, existuje několik výhod:
- Prvním a poměrně podstatným rozdílem je třída přesnosti, která je 7-9. Navíc je povrchová úprava získaného dílu vylepšena až na 3-6. Navíc se snižují přídavky, které jsou povoleny pro následné opracování výsledného dílu po odlití.
- Jedním z velkých plus je výrazné snížení mzdových nákladů na výrobu odlitků.
- Tato metoda odlévání snižuje spotřebu formovacích materiálů a také množství kovu díky skutečnosti, že je zmenšena velikost kanálů brány.
- Výrazně snížilo množství manželských výstupů.
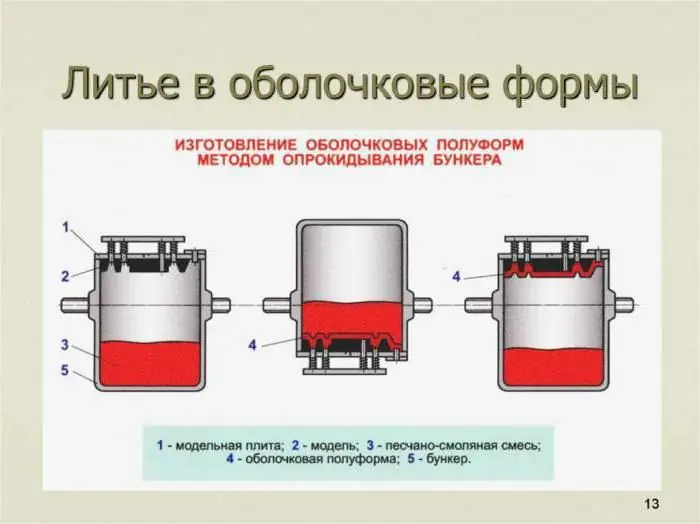
Odlévání do skořepinových forem má však určité nevýhody. Patří mezi ně:
- Životnost formy skořepiny - 1 odlitek.
- Náklady na formovací písek jsou poměrně vysoké.
- Vysoké procento škodlivých plynů.
Proces tvorby korpusu
Proces formování těla se provádí v šesti fázích:
- Prvním krokem je proces nalití směsi na rozžhavený kovový model a také proces udržování po dobu několika desítek sekund, dokud se kolem součásti nevytvoří tenká silná kůra. Nejčastěji jsou modely vyrobeny z litiny a jejich ohřev se provádí až na 230-315 stupňů.
- Poté je nutné provést operaci k odstranění přebytečného formovacího písku. Tloušťka kůry by nakonec měla být od 10 do 20mm. Záleží na době setrvání směsi na modelu a také na teplotě.
- Poté je nutné přenést modelovou desku spolu s formou do pece, kde budou až do konce vytvrzovacího procesu. Na konci tohoto postupu by měla být pevnost pláště mezi 2,4 a 3,1 MPa.
- Po vyjmutí z pece je vytvrzená skořepina vytlačena z desky. K tomuto postupu se používá speciální zatlačovač.
- Poté se dva nebo více modelů spojí dohromady pomocí nějaké svorky nebo lepením. Tyto formy lze použít pro odlévání do skořepinových forem nebo jednoduše skladovat. Téměř neomezená trvanlivost.
- Před zahájením procesu odlévání do hotové formy se do nich nalije brok, který pomáhá zabránit nebo zničit formu při dalším lití.
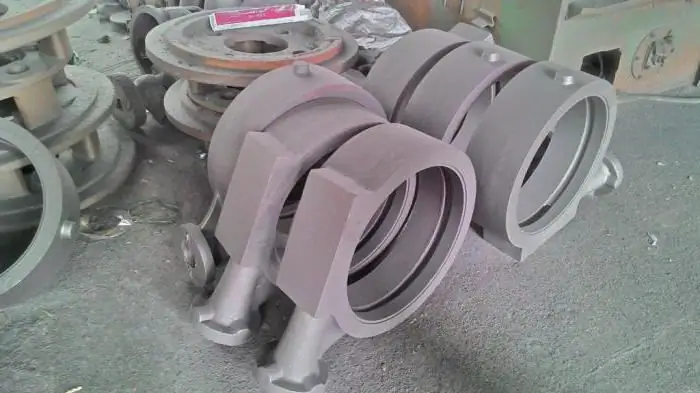
Podrobnosti o castingu
Vyplatí se začít tím, že typické tolerance, které jsou povoleny při výrobě nástrojů, mohou být 0,5 mm. Drsnost povrchu je povolena v rozsahu od 0,3 do 0,4 mikronů. Tyto limity jsou odůvodněny tím, že se používá jemnozrnný písek. Také stojí za zmínku: použití pryskyřice výrazně přispívá k tomu, že povrch je velmi hladký.
Objemy výroby
Abychom se mohli zapojit do výroby takových forem a dílů, je nutné se postarat o instalaci modelu formy. Doba potřebná k instalaci je méně než týden. Po dokončení instalace může výstupní množstvídosah 5 až 50 kusů za hodinu. Takové objemy výroby za hodinu jsou zcela reálné, k tomu je však nutné odpovídajícím způsobem připravit proces odlévání. Hlavní materiály, které budou vyžadovány pro odlévání, jsou litina, hliník, měď a také slitiny těchto druhů kovů. Dalším nezbytným materiálem bude slitina využívající hliník a hořčík.
Doporučuje:
Porterovy strategie: základní strategie, základní principy, vlastnosti
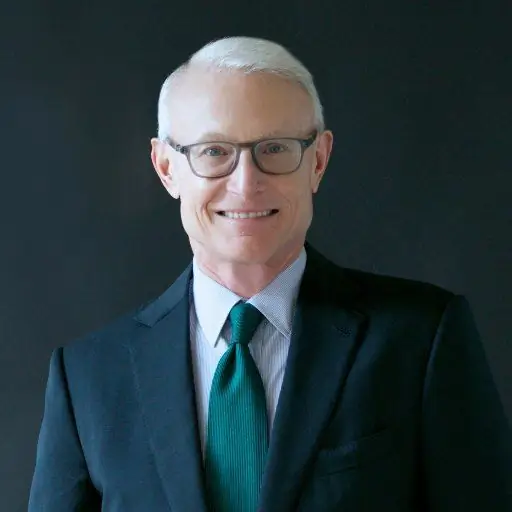
Michael Porter je uznávaný ekonom, konzultant, výzkumník, učitel, lektor a autor mnoha knih. kteří vyvinuli vlastní soutěžní strategie. Berou v úvahu velikost trhu a rysy konkurenčních výhod. Tyto strategie jsou podrobně popsány v článku
Moderní výroba. Struktura moderní výroby. Problémy moderní výroby

Rozvinutý průmysl a vysoká úroveň ekonomiky země jsou klíčovými faktory ovlivňujícími bohatství a blahobyt jejích obyvatel. Takový stát má velké ekonomické možnosti a potenciál. Významnou složkou ekonomiky mnoha zemí je výroba
Komerční banka. Funkce a základní operace
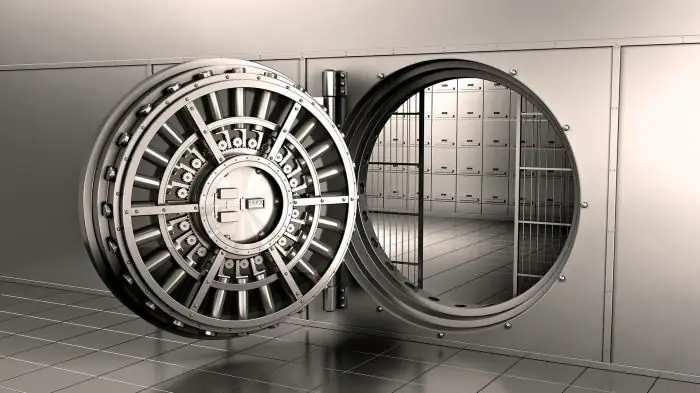
Důležitým článkem v bankovním systému je komerční banka. Funkce a hlavní operace této organizace jsou zaměřeny na dosažení maximální výše zisku
Odlévání do silikonové formy: zařízení. Vakuové lití do silikonových forem
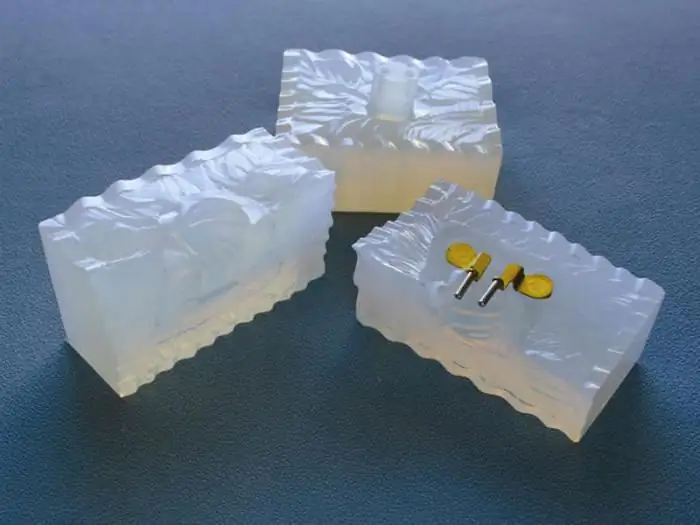
Pro výrobu malého počtu plastových polotovarů se nejčastěji používá vakuové lití do silikonových forem. Tato metoda je poměrně ekonomická (výroba kovové formy vyžaduje více času a peněz). Silikonové formy se navíc používají opakovaně a to také výrazně zlevňuje výrobu
Odlévání kovů: proces, metody, metody
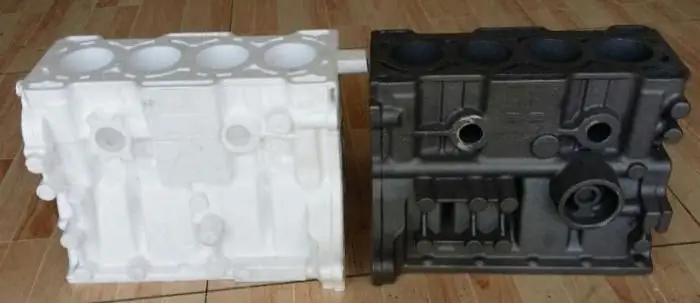
Kov je základem veškeré moderní civilizace. Moderní lidstvo za rok samo vytěží a zpracuje takové množství železa, že předtím by ho celý svět těžil minimálně pár století