2025 Autor: Howard Calhoun | [email protected]. Naposledy změněno: 2025-06-01 07:13
Vedoucí jakéhokoli podniku, bez ohledu na obor činnosti, sní o tom, že zisky rostou a výrobní náklady zůstávají nezměněny. K dosažení tohoto výsledku napomáhá systém „5S“ve výrobě (v anglické verzi 5S), který je založen pouze na racionálním využití vnitřních rezerv.
Tento systém nebyl vytvořen od začátku. Něco podobného na konci 19. století navrhl Američan Frederick Taylor. V Rusku to udělal vědec, revolucionář, filozof a ideolog A. A. Bogdanov, který v roce 1911 vydal knihu o zásadách vědeckého řízení. Na základě ustanovení v něm uvedených zavedl SSSR NOT, tedy vědeckou organizaci práce. Ale nejdokonalejší byl systém 5C navržený japonským inženýrem Taiichi Ohno a jím představený v závodě Toyota Motor ve výrobě. Co to je a proč se japonský systém stal tak populární?
Faktem je, že je založen na jednoduchém principu, který nevyžaduje náklady. Spočívá vdalší - každý zaměstnanec, od uklízečky po ředitele, by měl co nejvíce optimalizovat svůj podíl na celkovém pracovním postupu. To vede ke zvýšení zisku výroby jako celku a ke zvýšení příjmů všech jejích zaměstnanců. Nyní štafetu zavedení systému „5C“převzaly podniky po celém světě, včetně Ruska. V tomto článku se pokusíme přesvědčit skeptiky, že japonské know-how skutečně funguje, a to naprosto v jakékoli oblasti činnosti.
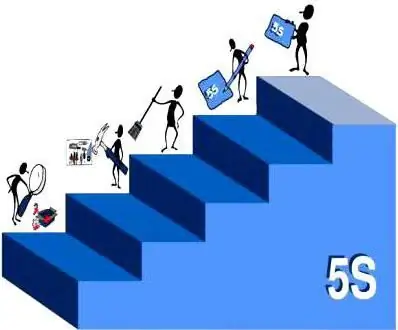
Systém „5C“ve výrobě, co to je
International 5S znamená pět kroků ("krok" v angličtině krok). Někteří ekonomové a propagátoři nového přístupu k práci vysvětlují název pěti japonskými postuláty, které jsou důsledně implementovány v systému 5S: seiri, seiton, seiso, seiketsu a shitsuke. Pro nás jsou bližší a srozumitelnější naše rodná „5C“- pět na sebe navazujících kroků, které je potřeba dokončit, abychom dosáhli prosperity naší výroby. Toto je:
1. Seřadit.
2. Udržování objednávky.
3. Udržování čistoty.
4. Standardizace.
5. Zlepšení.
Jak vidíte, systém „5C“nevyžaduje při výrobě nic nadpřirozeného. Možná proto se k ní stále můžeme setkat s nedůvěrou a lehkovážným přístupem.
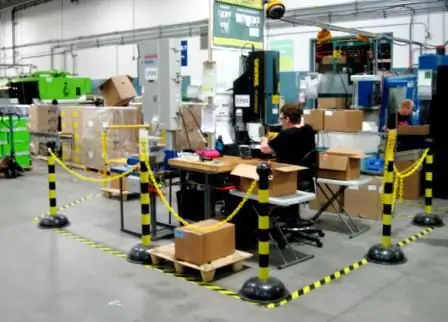
Fáze vytváření systému
Moudrý Japonec Taiichi Ohno, kterému se díky zavedení svých metod v továrně Toyota podařilo vystoupit zinženýr na generálního ředitele, si všiml, kolik ztrát vzniká v důsledku různých nekonzistencí a překrytí. Některé malé šrouby se například nestihly nasadit na dopravník a v důsledku toho se zastavila celá výroba. Nebo naopak, díly byly dodávány s marží, ukázaly se jako nadbytečné a v důsledku toho je jeden ze zaměstnanců musel odvézt zpět do skladu, což znamená ztrácet čas prázdnou prací. Taiichi Ohno vyvinul koncept, který nazval „just in time“. To znamená, že na dopravník bylo nyní dodáno přesně tolik dílů, kolik bylo potřeba.
Mohou být uvedeny další příklady. Systém „5S“ve výrobě zahrnoval i koncept „kanban“, což v japonštině znamená „reklamní nápis“. Taiichi Ohno navrhl připojit ke každému dílu nebo nástroji takzvaný „kanban“štítek, ve kterém byly uvedeny všechny potřebné informace o dílu nebo nástroji. V podstatě to platí na cokoliv. Například na zboží, léky, šanony v kanceláři. Třetím konceptem, na kterém je systém 5S ve výrobě založen, je koncept „kaizen“, což znamená neustálé zlepšování. Byly koncipovány i další koncepce, které byly vhodné pouze pro vysoce specializované výrobní procesy. V tomto článku je nebudeme uvažovat. Výsledkem všech v praxi prověřených inovací bylo vytvořeno 5 kroků použitelných pro jakoukoli výrobu. Pojďme je podrobně analyzovat.
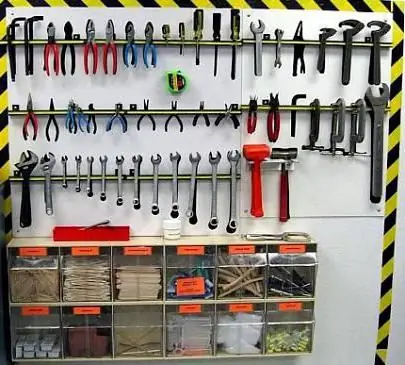
Třídění
Mnoho z nás má na svých počítačích položky, které vv podstatě není potřeba. Například staré formuláře, nepoužívané soubory, návrhy výpočtů, ubrousek, na kterém byl šálek kávy. A mezi tímto chaosem mohou být potřebné soubory nebo dokumenty. Mezi základní principy systému „5S“patří optimalizace vašeho workflow, tedy zajištění toho, abyste neztráceli čas hledáním správných věcí mezi troskami nepotřebného. Toto je třídění. To znamená, že na pracovišti (u stroje, na stole, v dílně - kdekoli) jsou všechny předměty rozloženy na dvě hromady - potřebné a nepotřebné, které je třeba zlikvidovat. Dále je vše, co potřebujete, rozloženo do následujících hromádek: „používané často a neustále“, „používané zřídka“, „téměř nepoužívané“. Tím je řazení dokončeno.
Udržování objednávky
Pokud položky pouze rozeberete, nebude to mít smysl. Tyto předměty (nářadí, dokumenty) je nutné uspořádat tak, aby to, co se používá neustále a často, bylo na očích, případně aby se to dalo rychle vzít a snadno vrátit. To, co se používá málo, lze poslat někam v krabici, ale musí se k tomu připevnit kanban tag, aby se to po chvíli dalo snadno a přesně najít. Jak vidíte, systém 5S na pracovišti začíná těmi nejjednoduššími kroky, ale ve skutečnosti se ukazuje jako velmi efektivní. A kromě toho zlepšuje náladu a chuť do práce.
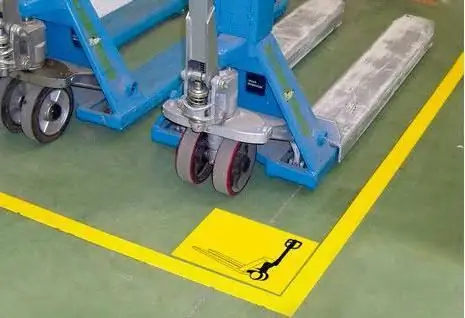
Udržování čistoty
Tento třetí krok je pro mnohé nejlogičtější. Od dětství nás učí být čistý. Nave výrobě je to také nutné a čisté by měly být nejen stoly kancelářských pracovníků nebo skříně ve stravovacích zařízeních, ale i stroje, technické místnosti uklízeček. V Japonsku se zaměstnanci o svá pracoviště vzorně starají, uklízejí se třikrát denně - ráno před prací, v poledne a večer, na konci pracovního dne. Kromě toho jejich podniky zavedly speciální značení oblastí, které jim umožňuje sledovat pořádek ve výrobě, to znamená, že oblasti hotových výrobků, skladování určitých dílů a tak dále jsou označeny různými barvami.
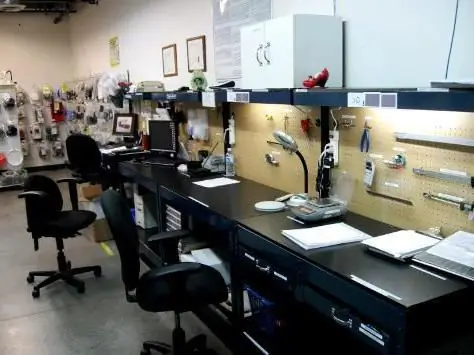
Standardizace
Principy standardizace vynalezl Taiichi Ohno. Hojně je využívá i moderní systém 5S. Řízení výroby díky standardizaci dostává úžasný nástroj pro řízení všech procesů. Díky tomu jsou příčiny zpoždění z harmonogramu rychle odstraněny a chyby, které vedou k uvolnění nekvalitních produktů, jsou opraveny. V závodě Toyota Motor standardizace vypadala takto: mistři sestavovali denní pracovní plány, na pracovišti byly vyvěšeny přesné pokyny a na konci pracovního dne speciální pracovníci kontrolovali, jaké odchylky od plánu během dne nastaly a proč. To je základní pravidlo standardizace, tedy přesné pokyny, plány práce a kontrola jejich plnění. Nyní mnoho podniků, například závody ENSTO v Estonsku, zavádí bonusový systém pro zaměstnance, kteří přísně dodržují ustanovení systému 5C a na základě toho zvyšují svou produktivitu, cožje velkou pobídkou k přijetí tohoto systému jako způsobu života.
Vylepšení
Pátý krok, který dokončuje systém „5S“ve výrobě, je založen na konceptu kaizen. Znamená to, že všichni zaměstnanci, bez ohledu na svou pozici, by měli usilovat o zlepšení pracovního procesu v oblasti, která jim byla svěřena. Filozofickou podstatou kaizenu je, že celý náš život se každým dnem zlepšuje, a protože práce je součástí života, neměla by ani ona zůstat stranou od zlepšení.
Pole působnosti je zde široké, protože dokonalost nezná hranic. Podle konceptů Japonců by sami pracovníci měli chtít zlepšit svůj výrobní proces, bez pokynů a nátlaku. Nyní mnoho organizací buduje týmy pracovníků, kteří sledují kvalitu produktů, učí ostatní své pozitivní zkušenosti a pomáhají dosahovat dokonalosti.
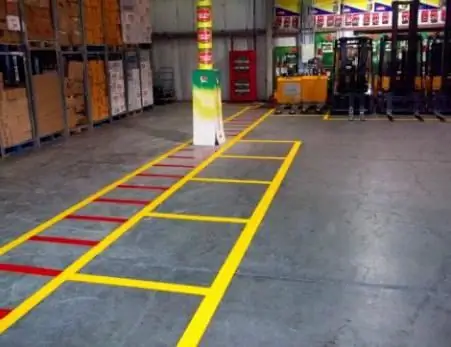
Základní chyby
Aby systém „5C“začal fungovat, nestačí jej zorganizovat nebo najmout zaměstnance, kteří donutí své kolegy k jeho implementaci. Je důležité, aby si lidé uvědomili užitečnost této inovace a přijali ji jako životní styl. Zavedení systému „5S“v Rusku do výroby naráží na potíže právě proto, že naše ruská mentalita je odlišná od japonské. Mnoho našich inscenací se vyznačuje následujícím:
1. Zaměstnanci, zvláště pokud pro ně neexistují žádné pobídky, se nesnaží zvyšovat zisky podniku. ptají se,proč se snažit udělat šéfa ještě bohatším, když už má všechno.
2. Samotní vedoucí nemají zájem o zavedení systému „5S“, protože v něm nevidí účelnost.
3. Mnoho direktiv „shora dolů“je zvyklých provádět pouze pro „tik“. V Japonsku mají k jejich práci úplně jiný přístup. Například stejný Taiichi Ohno, zavádějící systém „5S“, nemyslel na osobní zisk, ale na prospěch společnosti, ve které byl pouhým inženýrem.
4. V mnoha podnicích je systém 5S násilně zaváděn. Štíhlá výroba, která implikuje eliminaci ztrát všeho druhu (pracovní doba, suroviny, dobří zaměstnanci, motivace a další ukazatele), nefunguje, protože pracovníci se začínají na podvědomé úrovni bránit inovacím, což v konečném důsledku snižuje veškeré úsilí na nulu..
5. Manažeři implementující systém plně nechápou jeho podstatu, což způsobuje selhání v zavedených výrobních procesech.
6. Standardizace se často vyvine v byrokracii, dobrý skutek je zarostlý pokyny a směrnicemi, které jen překážejí práci.
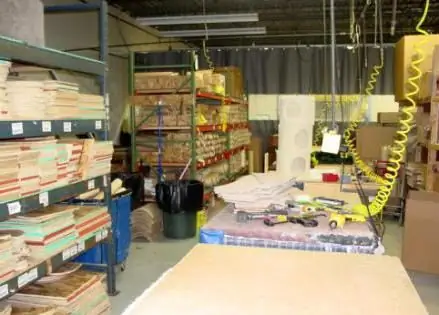
Recenze
Rusové, kteří zavedli systém „5S“do výroby, zpětná vazba na tuto novinku je velmi nejednoznačná. Zvýrazněné klady:
- lepší být na pracovišti;
- nerozptylujte se od práce zbytečnými maličkostmi;
- přehlednější pracovní postup;
- únava se na konci směny snížila;
- mírně zvýšenéplat zvýšením produktivity práce;
- snížil počet pracovních úrazů.
Významné nevýhody:
- při třídění nutí vše vyhodit;
- standardizace vedla ke zvýšení byrokracie;
- Zavedení systému „5C“nezhoršilo problémy ve všech oblastech podniku;
- Umístění systému 5S na první místo zastínilo důležité problémy, jako je nedostatek náhradních dílů.
Doporučuje:
Kuban červené plemeno kuřat: recenze, popis, vlastnosti, vlastnosti obsahu, krmení a péče
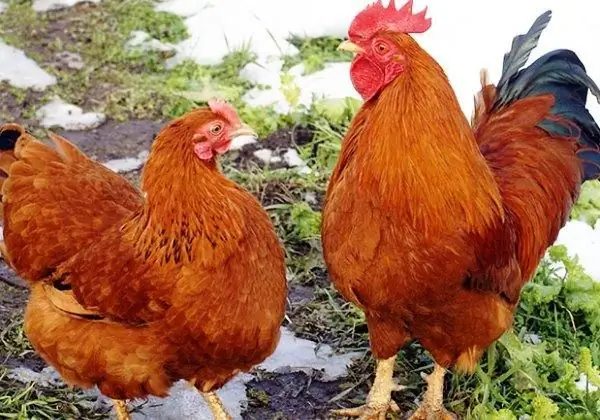
Podle četných recenzí má plemeno červených kuřat Kuban určité výhody i nevýhody. Charakteristickým rysem ptáka je dobrá produkce vajec, která zůstává přibližně na stejné úrovni, bez ohledu na sezónní faktory
Základní principy půjčování: popis, vlastnosti a požadavky
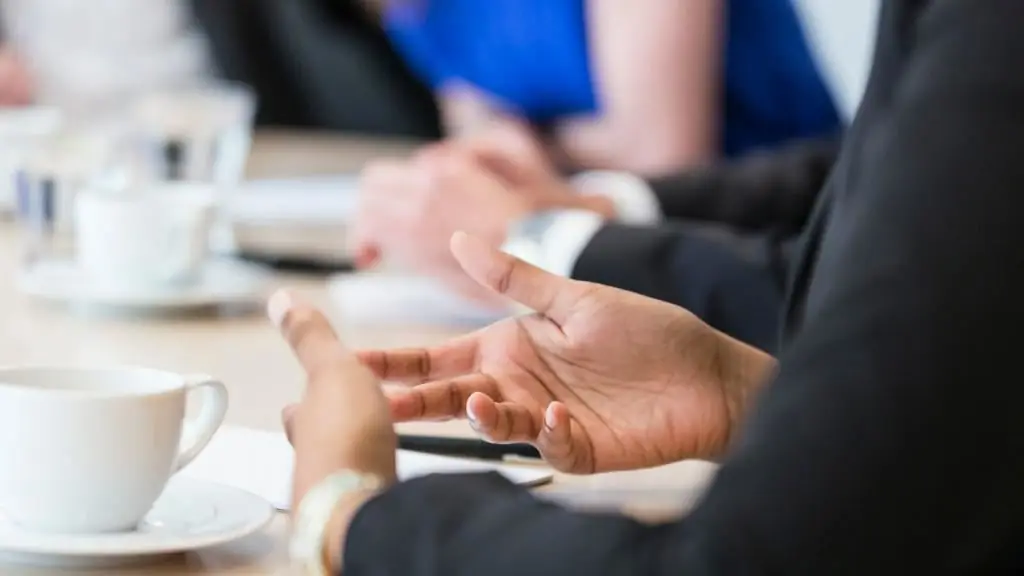
V naší těžké době jsou lidé často sužováni finančními problémy. Jedním z nejlepších řešení v této situaci je půjčka. Zjistěte, jaké jsou zásady půjčování a zda splňujete kritéria pro vzorného dlužníka
Tomato "Lady's man": recenze, popis, vlastnosti, vlastnosti pěstování
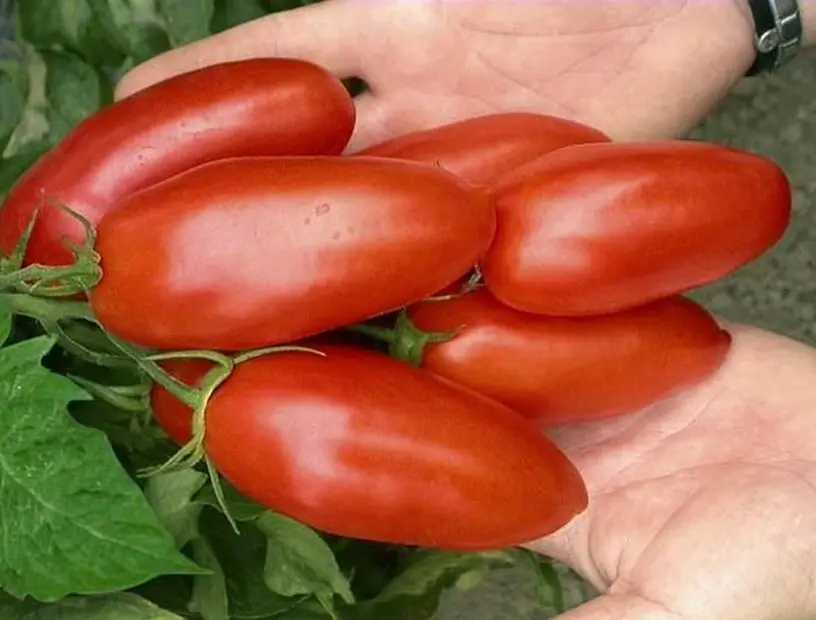
Odrůda rajčat "Lady's Man", jejíž recenze jsou mimořádně pozitivní, dnes vede mezi raně dozrávajícími rajčaty. Amatérští zahradníci, kteří alespoň jednou zasadili do svých záhonů, zůstali vždy fanoušky“
Protiletecký raketový systém. Protiletadlový raketový systém "Igla". Protiletadlový raketový systém "Osa"
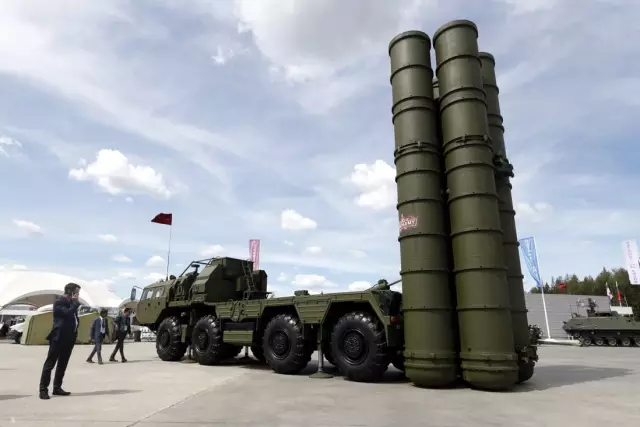
Potřeba vytvořit specializované protiletadlové raketové systémy dozrála během druhé světové války, ale vědci a zbrojaři z různých zemí se této problematice začali podrobně věnovat až v 50. letech. Faktem je, že do té doby prostě neexistovaly žádné prostředky k ovládání protiraketových střel
Účetnictví ve výrobě a jeho vlastnosti
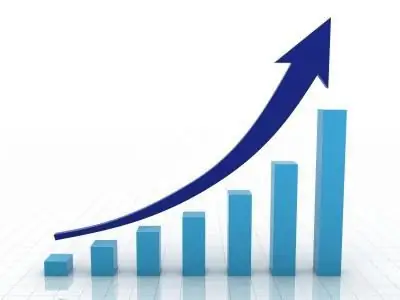
Účetnictví je nejdůležitějším směrem práce výrobního podniku. Na základě jakých principů to lze provést? Jaké jsou hlavní úkoly účetnictví ve výrobě?