2025 Autor: Howard Calhoun | [email protected]. Naposledy změněno: 2025-06-01 07:13
Zpožděné koksovací jednotky jsou nejběžnějším hardwarovým řešením pro rafinaci těžkých olejů. Jejich zařízení obsahuje 2 hlavní moduly - reaktor, kde se surovina zahřívá a koksuje, a mechanické zpracování. Projektování zařízení se provádí po etapách a zahrnuje výpočet a výběr procesního zařízení, stanovení technických a ekonomických ukazatelů.
Destination
Technologický proces koksování je jedním ze způsobů rafinace ropy. Jeho hlavním účelem je získávání velkého kusového ropného koksu. V průmyslu se používají 3 koksovací metody:
- Periodicky, krychle. Surovina se vloží do horizontálního zařízení, zahřeje se s topeništěm pod ním a poté se kalcinuje 2-3 hodiny. Poté se pec ochladí a hotový výrobek se vyloží. Tato metoda je nejjednodušší a nejméně produktivní.
- Nepřetržitý. Tato metoda je stále ve fázi průmyslového rozvoje.
- Polokontinuální, aktuálně přijatonejrozšířenější.
Ultra zpožděné koksovací jednotky jsou nejnovějším typem procesního zařízení. V nich se surovina předehřeje v peci a poté se přenese do nevyhřívaných reakčních komor, které mají tepelně izolační vrstvu pro udržení požadované teploty. Počet a velikost reaktorů, výkon pecí ovlivňují výkon celé elektrárny.
Provoz prvního DCU v Rusku byl zahájen v roce 1965 v Ufaneftekhimu. Zpožděná koksárna je v provozu dodnes. Po rekonstrukci v roce 2007 je jeho produktivita cca 700-750 tisíc tun/rok v přepočtu na hmotnost zpracovávaných surovin.
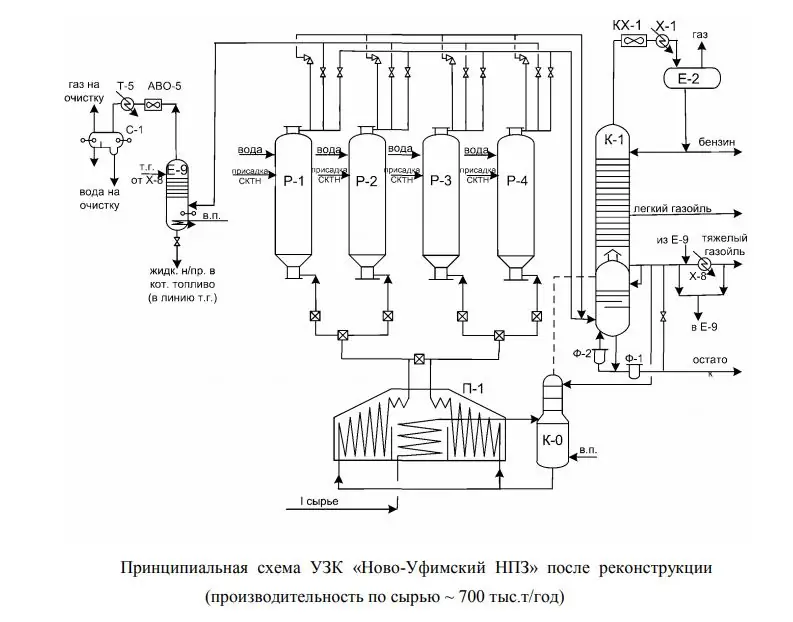
Konečné produkty
Následující látky byly získány ultrazvukovým testováním, kromě koksu:
- koksárenské plyny (používané jako technologické palivo nebo zpracované za účelem získání propan-butanové frakce);
- benzín;
- koksové destiláty (palivo, krakovací surovina).
Na domácích ultrazvukových testovacích strojích je výtěžnost koksu 20-30 % hmotnosti. Tento ukazatel závisí především na kvalitě surovin. Největší potřeba tohoto produktu je v metalurgickém průmyslu (výroba anod a elektrod, hliníku, brusiva, karbidů, uhlíko-grafitových materiálů, feroslitin). Kromě prvního Ufa DCU byly v Rusku postaveny další zpožděné koksovací jednotky: v rafinérii Omsk, rafinerie Novokujbyševsk, LLC LUKOIL-Volgogradneftepererabotka, LUKOIL-Permnefteorgsintez, LUKOIL-Permnefteorgsintez, v Angarské petrochemické společnosti, NOVOIL OJSC (Ufa), TANECO PJSC (Nizhnekamsk).
Suroviny
Potravinářské suroviny pro koksování se dělí do 2 skupin: produkty primárního a sekundárního zpracování. Následující látky se používají jako suroviny v jednotkách zpožděného koksování:
- topný olej;
- half-tar;
- tar;
- uhelný deht;
- asf alt a jiné průmyslové ropné produkty;
- tekutý uhelný zbytek;
- těžká pyrolýza a břidlicový dehet;
- zbytky tepelného krakování;
- ropný bitumen a těžké oleje.
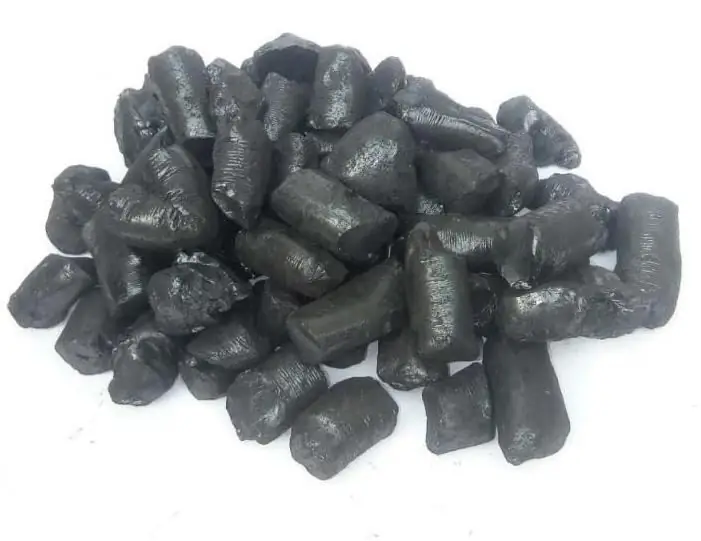
Vysoce aromatizované zbytky oleje jsou v současnosti nejběžnější surovinou.
Vliv na technologické parametry
Na vlastnostech vstupních surovin závisí následující parametry koksovny:
- účinnost reakční komory;
- kvalita obdržených produktů;
- vývod koksu;
- podmínky procesu.
Nejdůležitější parametry suroviny jsou:
- Koksování v závislosti na obsahu asf altopryskyřičných látek. Hodnota koksování by se měla pohybovat v rozmezí 10-20 %. S menší hodnotou se výtěžnost koksu snižuje a s větší se hromadí usazeniny uvnitř svitků v pecích. Koksovací kapacita je určena hmotností pevného zbytku v kelímku po zahřátí vzorku ropného produktu v kelímku.
- Hustota.
- Chemické složení. Zškodlivé nečistoty, které mají největší vliv na kvalitu koksu, uvolňují síru (neměla by být více než 1,5 % hmotnosti). V závislosti na účelu koksu v technologickém procesu je výhodné používat různé druhy surovin. Pro získání vláknité struktury konečného produktu se tedy používají materiály na parafínové bázi.
Výtěžnost koksu je úměrná hustotě vstupní suroviny a obsahu asf altenů.
Fáze koksování
Technologický proces v odložených koksovacích jednotkách je dlouhý a nepřetržitý, od dodávky surovin až po vyskladnění hotového výrobku. Obvykle se dělí do 3 fází:
- Rozkladné reakce, tvorba destilátových frakcí, meziprodukty, kondenzace.
- Významné snížení obsahu nenasycených uhlovodíků v plynech, zvýšení molekulové hmotnosti složek zbytku, cyklizační reakce.
- Zvýšení obsahu asf altenů ve zbytku až o 26 %, snížení množství pryskyřic a olejů. Převeďte kapalný zbytek na pevný koks.
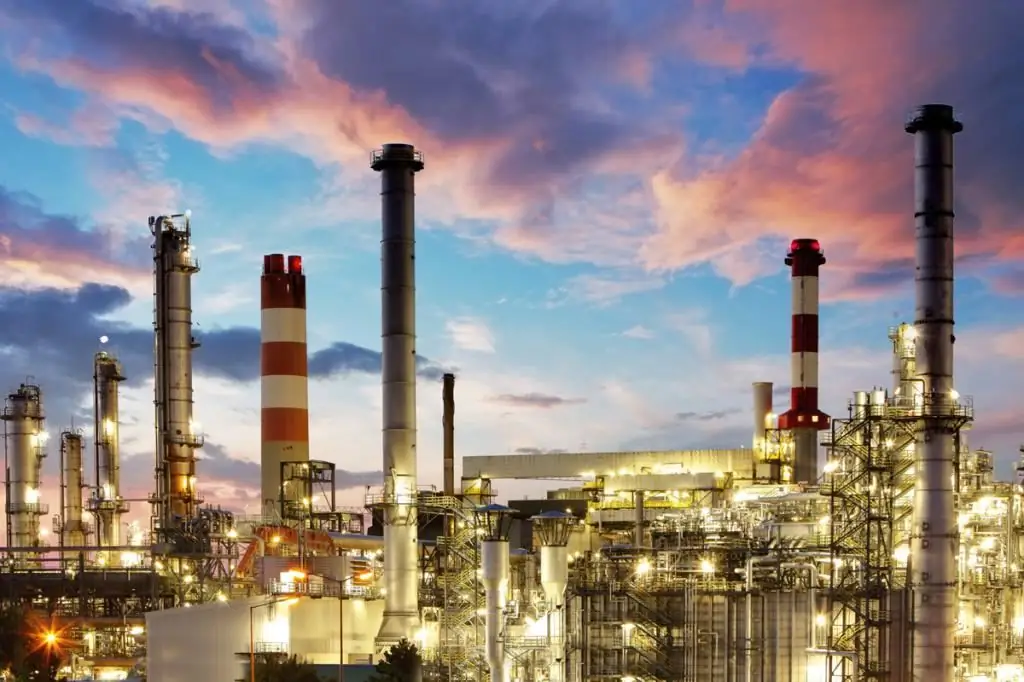
Klasifikace
Existují 2 hlavní typy zpožděných koksovacích jednotek podle jejich uspořádání: jednoblokové a dvoublokové.
Mezi dvoublokovými závody existují 4 typy, které se vyznačují následujícími konstrukčními a technologickými vlastnostmi:
- Vnitřní průměr koksovacích komor - 4,6 m. Stanové vyhřívací pece, čtyři komory pracující v párech. Kerosin a plynový olej získaný během procesu koksování se používají k vytápění.
- Colakomory Ø 5,5 m. Surovina - primární topné oleje s přídavkem vysoce aromatických uhlovodíků, které zvyšují výtěžnost kvalitního produktu.
- Reaktory z legované oceli Ø 5,5 m, výška 27,6 m, trubkové pece s volumetrickým nanášecím hořákem, horní ventily se zvýšeným průřezem, radioaktivní hladinoměry umožňující registraci místa fázové separace koks-pěny. Nejnovější inovace pomáhá lépe využít užitečný objem reaktoru. Dodávka turbulátorů s detergentními přísadami pro snížení koksování spirál, chlazený plynový olej v hlavových trubkách.
- Reakční komory Ø 7 m, výška 29,3 m. Axiální vstup suroviny do reaktorů, hydraulický systém pro vypouštění koksu s dálkovým ovládáním, elektrické jeřáby, sklady s podlahovým skladováním.
Použité vybavení
Zařízení, která jsou vybavena instalacemi tohoto typu, jsou rozdělena do následujících skupin podle účelu:
- Technologie, přímo zapojená do procesu koksování (pece, kolonové zařízení, tepelné výměníky, reaktorové komory, kostky, chladničky, čerpadla, potrubí, přístrojové vybavení, kohouty a další uzavírací a přepínací ventily).
- Odpadní voda - sběr a úprava vody pro návrat do pracovního cyklu (ochlazování a extrakce koksu).
- Zařízení pro vykládání koksu z komor (kostky). V moderních mechanizovaných instalacích může být mechanického a hydraulického typu (vazáky, navijáky, hřebeny, frézy, tyče, věže, pryžové manžety).
- Zařízení pro přepravu a zpracování hotového výrobku (příjmové skluzy a rampy, jeřáby, dopravníky, podavače, drtiče, sklady).
- Stroje a zařízení pro mechanizaci práce.
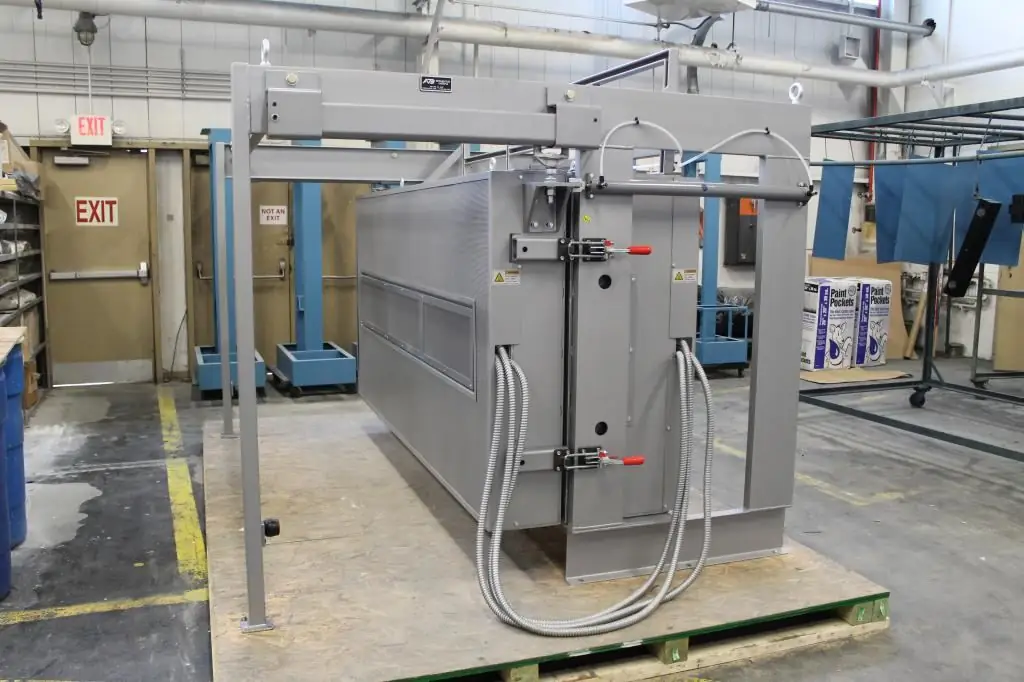
Při projektování zpožděných koksoven je nutné pečlivě zvážit konstrukci reakčních komor a pecí, protože délka pracovního cyklu závisí na spolehlivosti jejich provozu.
Parametry procesu
Hlavní parametry koksovací technologie jsou:
- Recirkulační poměr, definovaný jako poměr celkového zatížení reakčních hadů pecí k zatížení celého závodu z hlediska surovin. S nárůstem jeho hodnoty se zvyšuje výtěžnost vysoce kvalitního koksu, plynu a benzínu, ale klesá množství těžkého plynového oleje.
- Tlak v reakční komoře. Jeho pokles vede ke zvýšení výtěžnosti plynového oleje, snížení výtěžnosti koksu a plynu a zvýšení pěnivosti.
- Procesní teplota. Čím je větší, tím je koks kvalitnější z hlediska množství těkavých látek, jeho pevnosti a hustoty. Maximální hodnota je omezena rizikem koksování pece a potrubí, což snižuje životnost svitků. Každý druh suroviny má svou vlastní optimální teplotu.
Výstavba odložených koksárenských jednotek je spojena s vysokými investičními náklady. Nejčastěji se proto provádí rekonstrukce již fungujícího komplexu zařízení. Toho je dosaženo snížením cyklukoksování, zavádění nových reakčních komor nebo snížení recirkulačního poměru.
Princip fungování
Zpožděné koksovací jednotky se skládají z jedné nebo více spárovaných skupin komor, ve kterých jedna komora pracuje ve fázi výroby koksu a druhá při vykládce nebo v mezistavu. Proces rozkladu výchozího materiálu začíná v trubkové peci, kde se zahřeje na 470-510 °C. Poté surovina vstupuje do nevytápěných komor, kde je hluboce zkoksována díky teplu, které s ní přichází.
Plynné a kapalné uhlovodíky jsou vypouštěny pro frakční separaci v destilační koloně. Koks vstupuje do oddělení mechanického zpracování, kde se vykládá, třídí a přepravuje. Ve vrstvě hotového výrobku je vyvrtána studna a do ní je umístěna hydraulická řezačka. Jeho trysky pracují pod tlakem až 20 MPa. Kusy separovaného koksu padají na drenážní plošinu, kde je voda odváděna. Produkt je poté rozdrcen na menší kousky a rozdělen na frakce. Poté se koks přesune do skladu.
Princip schématu ultrazvuku je znázorněn na obrázku níže.
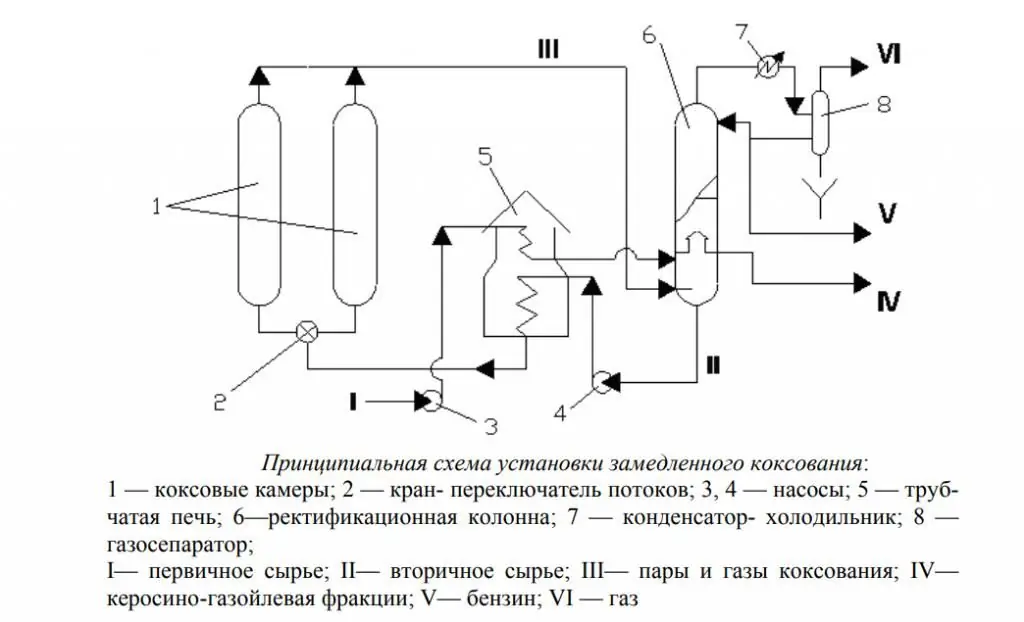
Kosové komory
Komory jsou reaktor, který je základem celé instalace. Cyklus provozu komory je obvykle 48 hodin, nicméně v posledních letech byla navržena ultrazvuková zařízení pracující v 18- a 36hodinovém režimu.
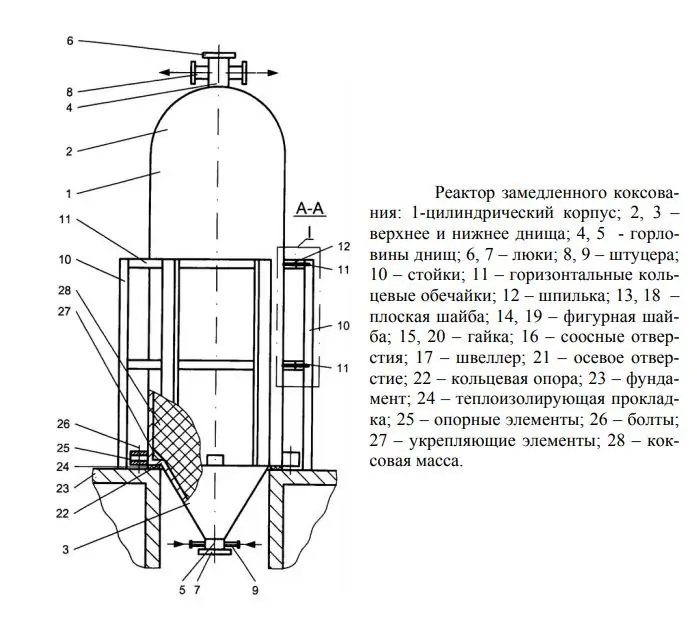
Jeden provozní cyklus reaktoru se skládá z následujících operací:
- nakládka surovin, proces koksování (1 den);
- off (1/2 hodiny);
- hydrotermální léčba (2,5 hodiny);
- vodní chlazení produktu, odstranění vody (4 hodiny);
- vyložit produkt (5 hodin);
- těsnění šachet, tlaková zkouška horkou párou (2 hodiny);
- topení olejovými parami, přepnutí na pracovní cyklus (3 hodiny).
Design
Projekt odložené koksovací jednotky je vyvíjen v následujícím pořadí:
- stanovení požadované produktivity, t/rok;
- analýza zdrojové základny;
- vypracování teoretické materiálové bilance procesu koksování pro různé druhy surovin;
- určení hlavních materiálových toků;
- vývoj konceptu instalace;
- zdůvodnění velikosti a počtu reaktorů;
- stanovení doby plnění jedné komory koksem a jeho hydraulický výpočet, sestavení harmonogramu provozu reaktoru;
- výpočty teplotního zatížení komory;
- výpočet konvekčních a radiačních komor;
- vývoj uspořádání výrobní linky;
- technologické výpočty dalších hlavních zařízení (destilační kolona, pece, chladničky atd.);
- vývoj monitorovacího a řídicího systému, výběr automatizačních nástrojů;
- popis schémat nouzové ochrany;
- rozvoj environmentálních aspektů a bezpečnostních opatření;
- stanovení ekonomických ukazatelů (kapitálové náklady, počet obsluhujícího personálu, mzdy,výrobní náklady na suroviny a pomocné materiály, roční ekonomický efekt, kalkulace produktu).
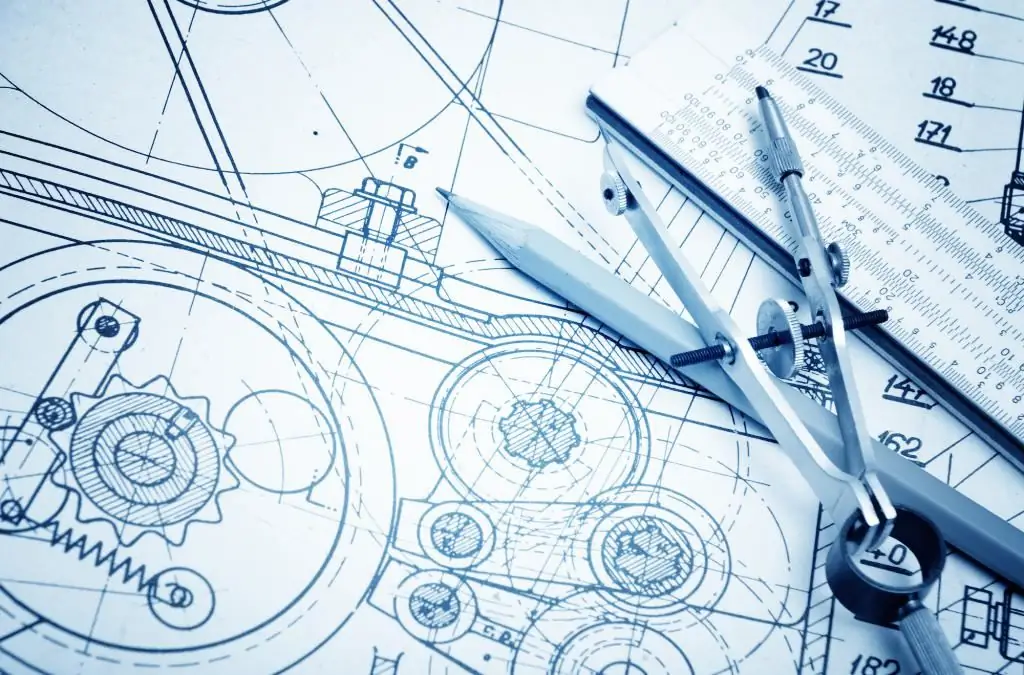
Výpočet kapacity zpožděné koksovací jednotky na roční bázi se provádí podle vzorce:
N=P x t, kde P je kapacita závodu, t/den;
t je počet pracovních dní v roce.
Výstup produktu ve fyzickém vyjádření podle možností základny a provedení je určen na základě materiálové bilance instalace.
Doporučuje:
Metody pro výpočet výrobních nákladů. Fixní náklady na jednotku výkonu
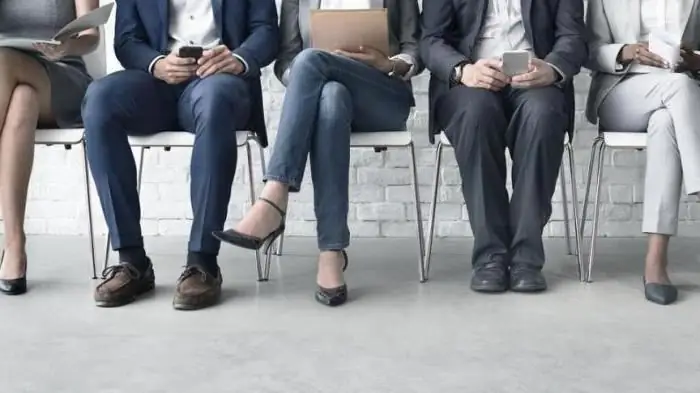
Výrobní náklady jsou důležitým ekonomickým ukazatelem, který odráží efektivitu výrobních činností. Proto je tak důležité umět správně provádět výpočty a vyvodit rozumné závěry. Podívejme se podrobněji na hlavní typy, metody výpočtu
Co je jalový výkon? Kompenzace jalového výkonu. Výpočet jalového výkonu
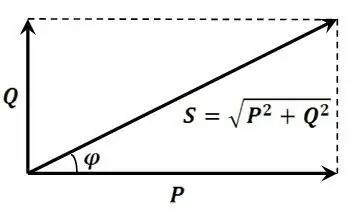
V reálných výrobních podmínkách převládá jalový výkon induktivní povahy. Podniky instalují ne jeden elektroměr, ale dva, z nichž jeden je aktivní. A za nadměrnou spotřebu energie „pronásledovanou“marně přes elektrické vedení jsou příslušné úřady nemilosrdně pokutovány
Inovativní projekt: příklad, vývoj, rizika a hodnocení výkonu. Inovativní projekty ve škole nebo v podnikání
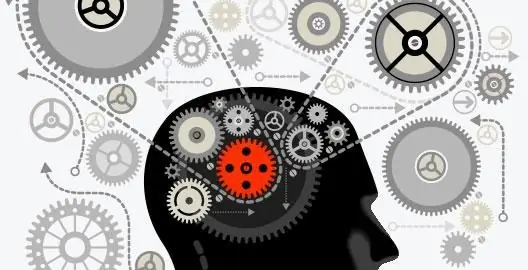
Inovativní projekt je komplexní systém akcí zaměřených na dosažení určitých cílů v rozvoji vědy a techniky. Propojují je vykonavatelé činností, termíny a zdroje. Inovační program je soubor vzájemně propojených inovačních projektů a projektů, které jsou zaměřeny na podporu aktivit v tomto směru
Třífázová síť: výpočet výkonu, schéma zapojení
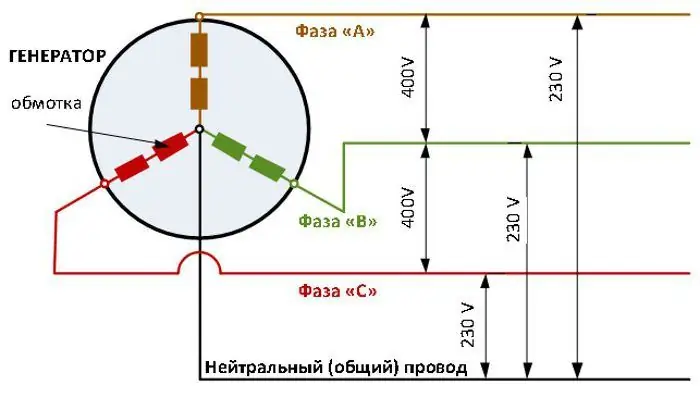
Při správném návrhu a údržbě je třífázová síť ideální pro soukromý dům. Umožňuje rovnoměrné rozložení zátěže mezi fázemi a připojení dalších spotřebičů energie, pokud to sekce elektroinstalace umožňuje
Produktivita buldozerů. Výpočet výkonu buldozeru
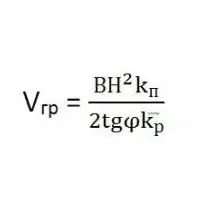
Při výstavbě jam, výkopů a násypů je vhodné použít buldozerovou sadu zařízení, pokud průměrný dosah podélného nebo příčného tažení nepřesahuje 100 metrů. Pro výběr nejoptimálnějšího modelu speciálního zařízení je nutné porovnat výkon buldozerů s různými trakčními třídami a různými typy pracovních zařízení