2025 Autor: Howard Calhoun | [email protected]. Naposledy změněno: 2025-06-01 07:13
Použití investičních modelů je poměrně oblíbenou metodou slévárenské výroby. Metoda se vyznačuje složitostí technologického procesu a vysokými mzdovými náklady na přípravné procesy. Proto se používá tam, kde je potřeba přesně dodržet rozměry a zajistit vysokou kvalitu povrchu dílů. Takto se odlévají lopatky turbín a vysoce výkonné nástroje, zubní protézy a šperky, stejně jako sochy složité konfigurace. Podstatou lití do ztraceného vosku je, že forma pro odlévání je jednodílná, model nízkotavitelných materiálů se při formování neodstraňuje, ale taví. Tím je zajištěno pečlivé dodržení rozměrů a reliéfu. Kov se nalije do dutiny zbývající z modelu. Po dokončení chlazení se forma zničí a produkt se odstraní. Při odlévání velkých sérií se náklady na výrobek snižují.
Výhody metody
Hlavní výhodou investičního lití je přesnost přenosu formy a nízká drsnost povrchu. Kromě toho jsou k dispozici další výhody:
- Dostupná výroba lehce opracovaných slitinových dílů.
- Snižuje potřebu dalšího obrábění.
- Výrobky jsou odlévány, které by jinak musely být vyrobeny po částech a sestaveny dohromady.
- U velkých sérií je dosaženo snížení specifické pracovní náročnosti (na jeden výrobek) a jeho nákladů.
- Možnost mechanizace a částečné automatizace přípravných operací samotného odlévání.
Tyto přednosti činí metodu jednou z nejoblíbenějších a nejpoužívanějších v dnešní metalurgii, zejména v kombinaci s moderními progresivními metodami odlévání.
Nevýhody investičního odlévání
Nepochybné výhody této metody, jak se zdá, měly zajistit její dominanci mezi ostatními metodami. Navzdory popularitě metody investičního lití však nevýhody brání jejímu širokému přijetí. Hlavní nevýhodou je složitost vícestupňového procesu. Vyžaduje poměrně složité a nákladné technologické vybavení pro přípravné fáze. U jednoduchých produktů vyráběných v malých sériích má tato metoda vyšší náklady.
Pro nákladově efektivní aplikaci investičního lití jsou porovnány výhody a nevýhody metody, rozhodnutí ojeho výběr se provádí na základě posouzení poměru cena / kvalita. Proto se používá především u nejkritičtějších a nejdražších výrobků, které je obtížné získat jiným způsobem, jako jsou lopatky turbín, sochy, vysokorychlostní nástroje atd. Další oblastí použití jsou velkorozměrové odlitky, v který efekt měřítka umožňuje dosáhnout výrazného snížení nákladů.
Technology
Technologie investičního lití je vícestupňový výrobní proces, který je relativně náročný na práci. V první fázi je vyroben master model, který se stane standardem pro výrobu pracovních modelů poté, co projde všemi fázemi konečného produktu. Pro výrobu mistrovského modelu se používají jak speciální modelové kompozice, tak tradiční - sádra nebo dřevo. Materiál hlavního modelu by měl spojovat pevnost a snadnost zpracování.
Technologie investičního lití dále umožňuje vytvoření formy, do které budou odlévány všechny fungující modely. Formy jsou vyrobeny ze sádry, pryže, silikonu, méně často z kovu. Konstrukčně musí být nutně odnímatelné a určené pro opakované použití. Forma se naplní modelovou kompozicí, po vytvrdnutí se rozebere a sejme se další funkční model.
Při výrobě jedinečných dílů nebo malých sérií se fáze vytváření hlavního rozvržení a formy přeskakují a rozvržení (nebo několik) se vytvoří ručním lisováním materiálu.
Dalším krokem v procesu investičního lití jevýroba kolem rozložení (nebo bloku rozložení) licí formy. Tyto matrice jsou konstrukčně již neoddělitelné a jednorázové, což umožňuje dosáhnout pečlivého dodržení rozměrů a drsnosti výrobku. V moderním průmyslu se používají dva typy forem - tradiční pískovcové formy pro lití do zemních a skořepinové formy - pro výrobu přesných a drahých dílů.
Po dokončení formy se z ní model vytaví zahřátím nebo vyfouknutím přehřátou párou. Formy skořápky jsou dodatečně zpevněny zahřátím až na 1000 ˚С.
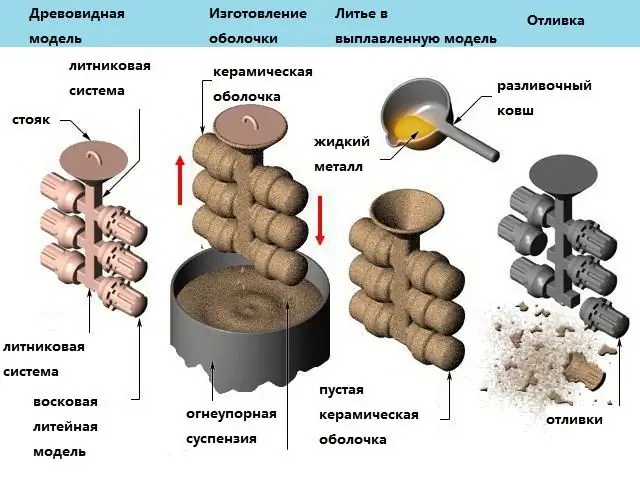
Konečná fáze procesu zahrnuje vlastní odlévání výrobku, jeho chlazení v přírodních podmínkách nebo speciální metodou v termostatu, destrukci formy a čištění výrobku. Metoda umožňuje získat vysoce kvalitní odlitky o hmotnosti od několika gramů do desítek kilogramů.
Sestavy modelů
Materiál pro výrobu layoutu musí mít určité vlastnosti. Mělo by mít vlastnosti jako:
- Plasticita v pevné fázi. Je nutné přesně zopakovat tvar budoucího výrobku a v případě potřeby jej opravit.
- Síla. Model musí bez deformace vydržet proces vytváření tvaru kolem něj.
- Tavitelné. Vykreslení modelu by nemělo vyžadovat mnoho času a energie.
- Roztavená tekutost. Kompozice by měla snadno proniknout do všech prohlubní a detailů reliéfu a přesně opakovat obrysy budoucího detailu.
- Ekonomika. Zvláště důležité pro velkosériovou výrobu.
Pro modelové kompozice se obvykle používá směs stearinu a parafínu. Tyto materiály se vzájemně úspěšně doplňují svými parametry, kompenzují nedostatečný bod tání parafínu a nadměrnou viskozitu stearinu.
Složení na bázi lignitového vosku jsou v tomto odvětví neméně populární. Jeho hlavními vlastnostmi jsou odolnost proti vlhkosti, pevnost a schopnost vytvářet velmi hladké povlaky, což je cenné zejména pro modelování výrobků.
Sloučeniny sestávající ze směsi hnědouhelného vosku, parafínu a stearinu.
Výroba forem
Pro výrobu unikátních produktů se layout připravuje vyříznutím kusu modelové hmoty ručně nebo podle šablon. Na soustruzích se vyrábí i modely v podobě rotačních těles. V poslední době se stále více rozšiřuje metoda 3D tisku modelů. Je vhodný jak pro jednotlivá rozložení, tak pro malé série.
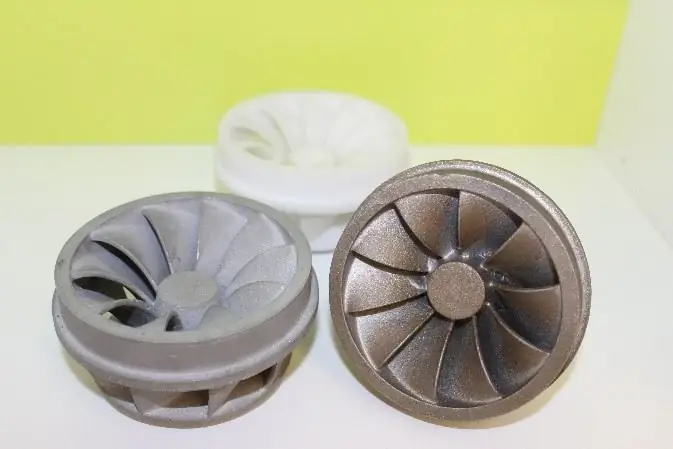
Náklady na moderní průmyslovou 3D tiskárnu jsou stále vysoké, ale díky snadné rekonfiguraci z jednoho produktu na druhý se může stát efektivním nástrojem pro tvorbu modelů v případě velkého počtu heterogenních malosériových zakázek.
Aby bylo možné vytvořit velké množství stejných rozložení, je matrice vyrobena ze sádry, pryže, silikonu nebo kovu. Pracovní layouty jsou zase vyráběny litím do matrice. Podle návrhu musí být forma skládací, aby byla zajištěna možnost výroby daného počtu modelů. Zvolený materiál by měl také poskytovat takovou příležitost, proto jsou na něj kladeny takové požadavky, jako je pevnost, hustota, nízká drsnost a chemická inertnost ve vztahu k uspořádání. Formovací hmota musí mít také minimální přilnavost k maketě, aby bylo zajištěno, že hotové makety lze snadno odstranit a dodržet rozměry. Důležitou vlastností formy je její pevnost a odolnost proti opotřebení, zejména u velkých sérií.
Vytváření modelů a bloků
Široce používanou metodou výroby investičních modelů je jejich odlévání pod nízkým tlakem do forem. Vstřikování kapalné směsi se provádí jak ručně, pomocí pístových stříkaček, tak i mechanickými, hydraulickými nebo pneumatickými kompresory. V případě použití hnědouhelného vosku je nutné zahřát potrubí pro přívod kompozice z důvodu její vysoké viskozity. Modely z expandovaného polystyrenu jsou vyráběny vytlačováním na automatických formovacích strojích.
Pro zvýšení ekonomické efektivity a snížení pracnosti v případě sériové výroby malých odlitků jsou jejich dispozice kombinovány do bloků. Vtokové systémy se tvoří nad bloky přichycením jednotlivých dispozic k vtokům pomocí ruční páječky. V případě jednotlivých odlitků nebo malých sérií jsou modely vyráběny ručně.
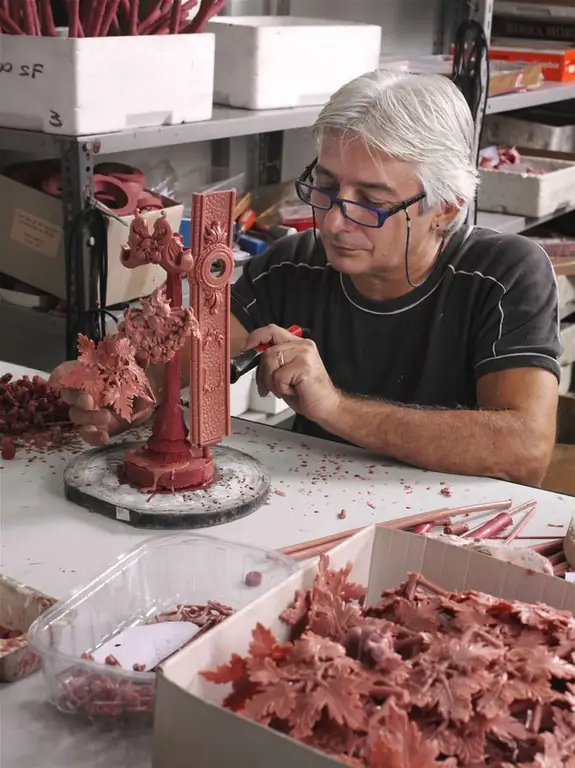
Při formování vtokových systémů je nutné zajistit neturbulentní proudění taveniny, rovnoměrné plnění všech prvků matrice. Při plnění formuláře z PGS musíte také sledovat rovnoměrné vyplnění všechotvory mezi vtoky a zabránění poškození.
Vytvoření formy
V uvažované metodě lití na vytavitelný materiál existují dva hlavní typy forem:
- Směsi písku a jílu (SGM).
- Shell.
Odlévací formy na odlévání vosku se používají především při výrobě malých sérií výrobků, které nevyžadují příliš vysokou přesnost. Proces jejich výroby je poměrně pracný a vyžaduje vysokou a často unikátní zručnost modelářů a formařů. Částečná mechanizace se hodí pouze pro určité operace, jako je příprava a plnění formovacího písku, jeho pěchování.
Skořepinové formy se na druhé straně používají k výrobě dílů, které vyžadují zvláštní výrobní přesnost. Proces jejich výroby je složitější a zdlouhavější, ale hodí se lépe k mechanizaci.
Ground casting
Toto je nejstarší metoda zpracování kovů, kterou lidstvo zvládlo. Naši předkové ji ovládali současně s počátkem používání kovových výrobků jako zbraní, nástrojů nebo náčiní, tedy asi před 5 tisíci lety. Roztavený kov se nalije do připravené matrice ze směsi písku a jílu. Nejstarší místa pro zpracování kovů vznikla právě tam, kde se poblíž nacházela ložiska kovů ve formě nugetů a rýžovišť. Typickým příkladem je závod Kasli na Uralu, světově proslulý svým litím železných krajek.
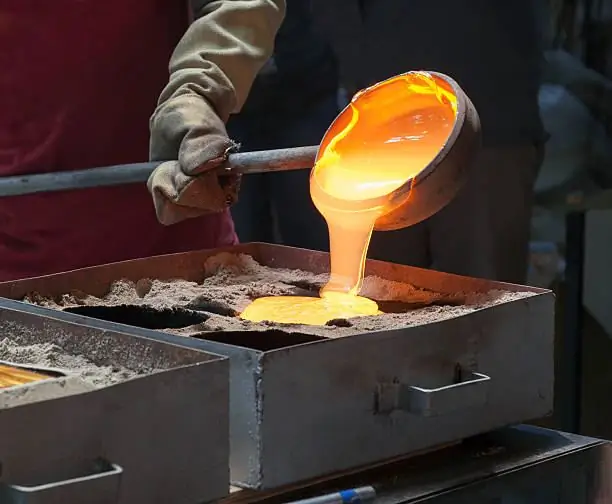
Metoda vytavitelného lití se používá pro výrobu kovových výrobků - železných i železnýchbarevný. A pouze pro kovy, které vykazují zvýšenou tendenci reagovat v kapalné fázi (jako je titan), je nutné vyrábět matrice z jiných složení.
Výrobní proces odlévání v PGS se skládá z následujících fází:
- modelářství;
- příprava baňky;
- naplnění a zhutnění směsi v baňce;
- odlévání kovů;
- vyjmutí a vyčištění odlitku.
Formulář od ASG - jednorázové použití. Chcete-li získat hotový výrobek, bude muset být rozbit. Zároveň je většina směsi k dispozici pro opětovné použití.
Jako materiály pro ASG se používají směsi převážně křemenných písků různé zrnitosti a plastické jíly, jejichž obsah se pohybuje od 3 do 45 procent. Takže například umělecké odlitky se vyrábějí za použití směsi s obsahem 10-20% jílu, u zvláště velkých odlitků je obsah jílu upraven na 25%.
Používají se dva podtypy:
- Obkladové směsi. Jsou umístěny na vnitřním povrchu formy a interagují s roztaveným kovem. Musí být žáruvzdorné, nezničitelné teplotními rozdíly az toho vyplývajícím namáháním. Tyto směsi mají jemné zrno, aby pečlivě přenesly detaily povrchu. Schopnost směsi propouštět plyn je také velmi významná.
- Směsi na plnění. Používají se pro zásyp mezi lícovou vrstvou a stěnami baňky. Musí odolat hmotnosti litého kovu, zachovat tvar výrobku a přispět k včasnému a úplnému odstranění plynů. Vyrábí se z levnějších druhů písku,opakovaně použitelné.
Pokud licí plyny neunikají hmotou formovacího písku, ale vtokovým systémem, dochází k defektům v odlitku, které vedou ke sňatku.
Tradiční technologie lití do země je podrobně ilustrována ve filmu A. Tarkovského "Andrei Rublev". V povídce „Zvon“vede mladý muž Boriska, syn zesnulého mistra, slévárenský artel a odlévá kostelní zvon.
Odlévání mušle
Metoda vytavitelného lití do skořepinových forem se vyznačuje nejlepším přenosem rozměrů výrobku a nízkou drsností povrchu. Model je vyroben z tavitelných sloučenin, jako je hnědouhelný vosk. Slévárny také široce používají složení parafín-stearin ve stejných poměrech. V případě odlitků velkých rozměrů jsou do materiálu modelu zahrnuty soli, které chrání model před deformací. Ponořením do roztoku se model pokryje v 6-10 vrstvách vysokoteplotní suspenzí.
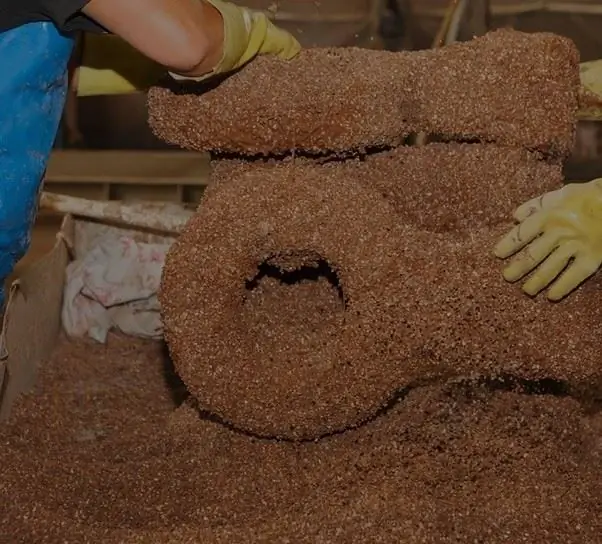
Hydrolyzované silikáty působí jako pojivo, elektrokorund nebo krystaly křemene jsou brány jako žáruvzdorný posyp. Materiály skořepinových forem se vyznačují vysokou pevností, nízkou hygroskopicitou a vynikající propustností pro plyny.
Rozložení se suší v atmosféře plynného čpavku. V další fázi se forma zahřeje na 120 ˚C, aby se odstranil parafínový model. Zbytky směsi se odstraní přehřátou párou pod vysokým tlakem. Dále je forma kalcinována při teplotách do 1000 ˚С, což vede k její konečné fixaci a odstranění látek,které se mohou uvolňovat jako plyny během procesu odlévání.
Plášť je umístěn v jakési baňce, která je pokryta ocelovými broky. To pomáhá zachovat konfiguraci při plnění formy taveninou a zároveň zlepšuje podmínky pro chlazení odlitku. Tavenina se nalévá do forem vyhřátých na 1000 ˚С. Po ochlazení výrobku podle speciálního programu v termostatu se forma zničí, odlitek se vyjme a vyčistí.
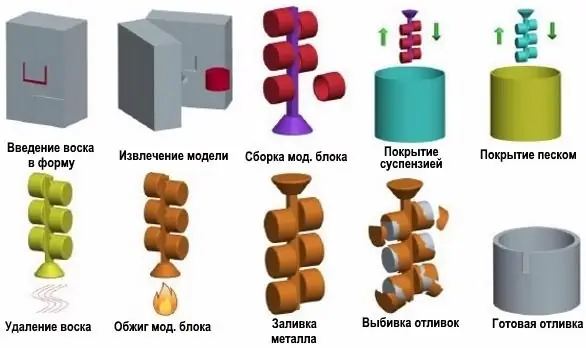
Hlavní výhodou této metody odlévání je vysoká rozměrová přesnost a nízká drsnost povrchu.
Další výhody metody:
- Odlévání dílů ze slitin, které se obtížně obrábí.
- Odlévání předmětů, které by jinak musely být odlévány po částech a poté složeny zpět.
Nevýhody této metody vytavitelného lití jsou nízké využití kovu a zvýšená pracnost.
Přesné lití
Přesné lití na vytavitelný materiál - tak se nazývá technologie i samotný finální produkt. Vysoká přesnost odlévání je zajištěna tím, že při přípravě formy není potřeba z ní vytahovat model výrobku. Při použití tradiční metody je výroba licí matrice složitý a časově velmi náročný vícestupňový proces. To platí zejména v případě odlitků složitých konfigurací s prohlubněmi, prohlubněmi a vnitřními dutinami.
Například při odlévání litinové nebo měděné vázy s proměnným zakřivením povrchu musíte použít spoustu triků. Ano, prvníspodní polovina baňky se naplní, poté se model vyjme, převrátí a horní polovina se zatluče. Model musí být kompozitní, držadla vázy jsou ze dvou prvků, vytahují se dutinou modelu ve dvou fázích - nejprve spodní prvek, poté horní. Všechna tato četná otáčení a tažení nemohou mít pozitivní vliv na celistvost povrchu formy a v konečném důsledku ani na přesnost dodržení rozměrů odlitku a kvalitu jeho povrchu. Kromě toho zůstává problém s přesným slícováním částí baněk a jejich bezpečného připevnění k sobě.
Výroba přesného odlitku těchto nedostatků postrádá, nevyžaduje tak vysoce kvalifikované modeláře a výrazně snižuje pracnost operací předlití. To je zvláště výrazné u velkých sérií odlitků.
Metoda umožňuje dosáhnout 2.-5. třídy přesnosti podle GOST 26645-85. To umožňuje odlévat vysoce přesné produkty, jako jsou lopatky turbín, řezné nástroje, včetně vysoce výkonných fréz a vrtáků, kritické vysoce zatížené držáky, malé vysoce zatížené části vozidel, obráběcí stroje a další složité mechanismy.
Vysoká rozměrová přesnost a vysoká třída povrchu minimalizují potřebu dalšího opracování odlitku, což šetří kov a snižuje výrobní náklady.
Zařízení
Potřebné vybavení pro investiční lití je různé a složité. Podniky je spojují do jediného a dobře koordinovaného komplexu,organizované jako místo, dílna nebo samostatná výroba.
Složení komplexu závisí na rozsahu výroby, velikosti, konfiguraci a oběhu odlitků.
Při výrobě zubních protéz a šperků tedy bude vybavení zahrnovat:
- modelový stůl;
- muflová pec s termostatem;
- sada skalpelů a špachtlí pro korekci tvaru modelu;
- formovací deska;
- baňka;
- nádrže na skladování a přípravu formovacího písku;
- sada pískových pěchovadel;
- kelímek na tavení kovu;
- kleště;
- kladivo k rozbití formy.
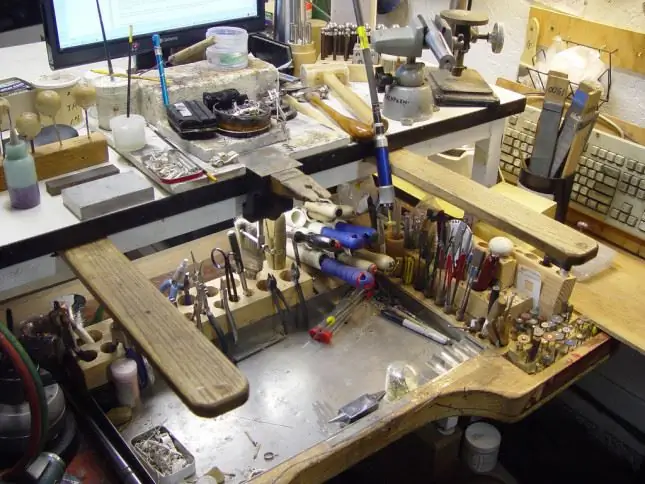
Tento výrobní komplex se snadno vejde na jeden stůl a do jedné skříně. Pokud se plánuje hromadná výroba například hliníkových odlitků - částí zařízení, bude vyžadováno vybavení pro:
- tvarování a lití keramických forem;
- sušicí formy;
- roztavení materiálu modelu a nanesení tepelně odolné vrstvy;
- čištění odlitků od formovací hmoty.
A konečně vlastní zařízení slévárenského komplexu, určené k získávání taveniny a její lití do formy. Může to být odlévací zařízení:
- pod nízkým tlakem;
- odstředivé;
- obvyklým způsobem gravitace.
Vstřikovací lisy a odstředivé lití stroje jsou samostatné vysoce mechanizované a automatizovanévýrobní komplex, izolovaný od atmosféry obchodu. Minimalizují manuální práci a vystavení člověka škodlivým podmínkám. Utěsněné komory, ve kterých jsou komplexy umístěny, zajišťují úplné zachycení a čištění výfukových plynů, což výrazně zvyšuje šetrnost podniku k životnímu prostředí.
Odlévání do ztraceného vosku má poměrně vysoký potenciál pro rozvoj, zvláště v kombinaci s pokročilými technikami výroby forem a lití.
Doporučuje:
Gravírování do plexiskla: výhody a nevýhody, technologie, vybavení
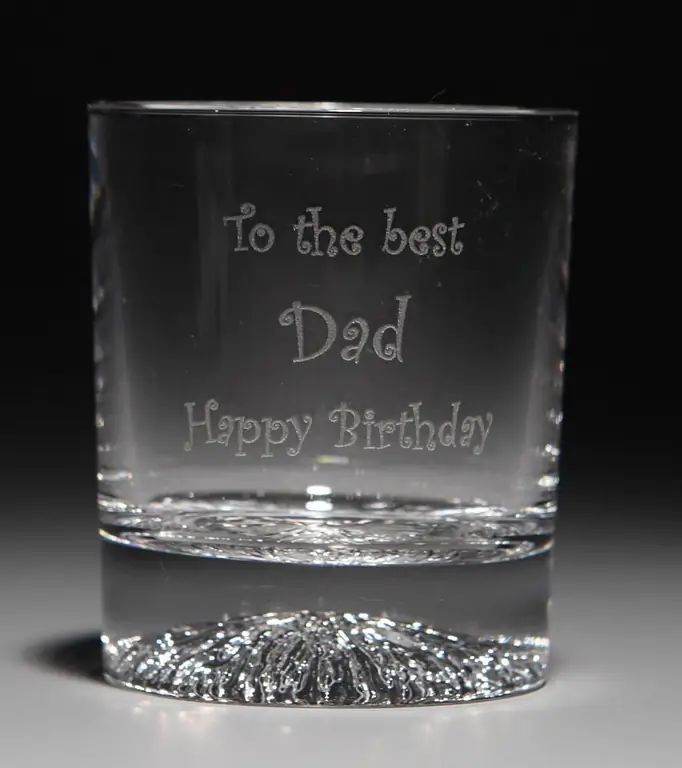
Gravírování do plexiskla je považováno za malířské řemeslo. Suvenýrová figurka, vitráže nebo skleněný stůl, které jsou zdobeny nádhernými kresbami, ztělesňují jemný umělecký vkus. Technologie moření a pískování jsou minulostí. Dnes může každý člověk s pomocí laserového stroje vytvořit vysoce detailní vzor
Knihtisk je Technologie knihtisku, moderní fáze vývoje, potřebné vybavení, výhody a nevýhody tohoto typu tisku
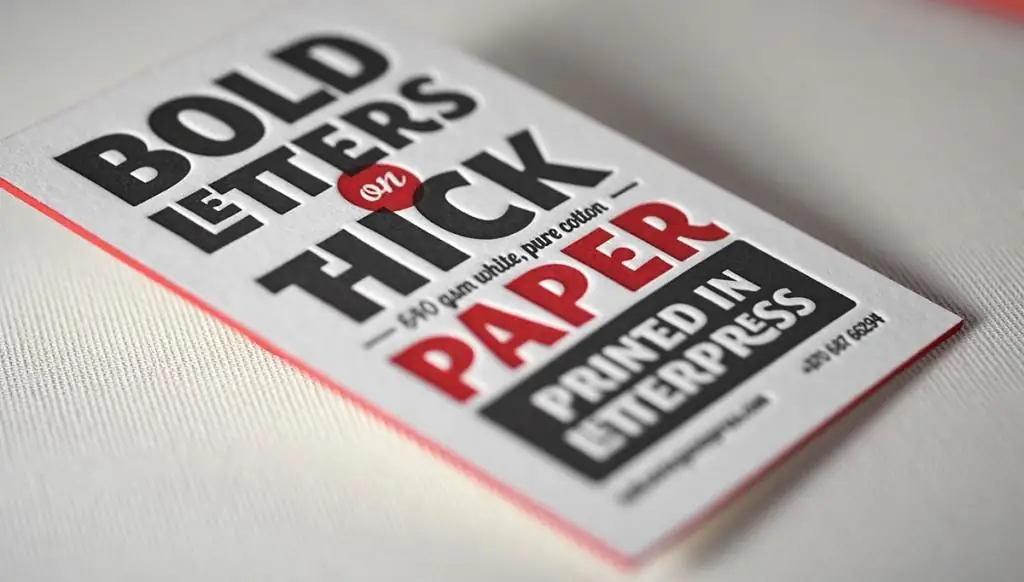
Knihtisk je jednou z typických metod aplikace informací pomocí reliéfní matice. Prvky, které vyčnívají, jsou pokryty barvou ve formě pasty a poté přitlačeny k papíru. Tak se replikují různá masová periodika, příručky, knihy a noviny
Ultrazvukové zpracování: technologie, výhody a nevýhody
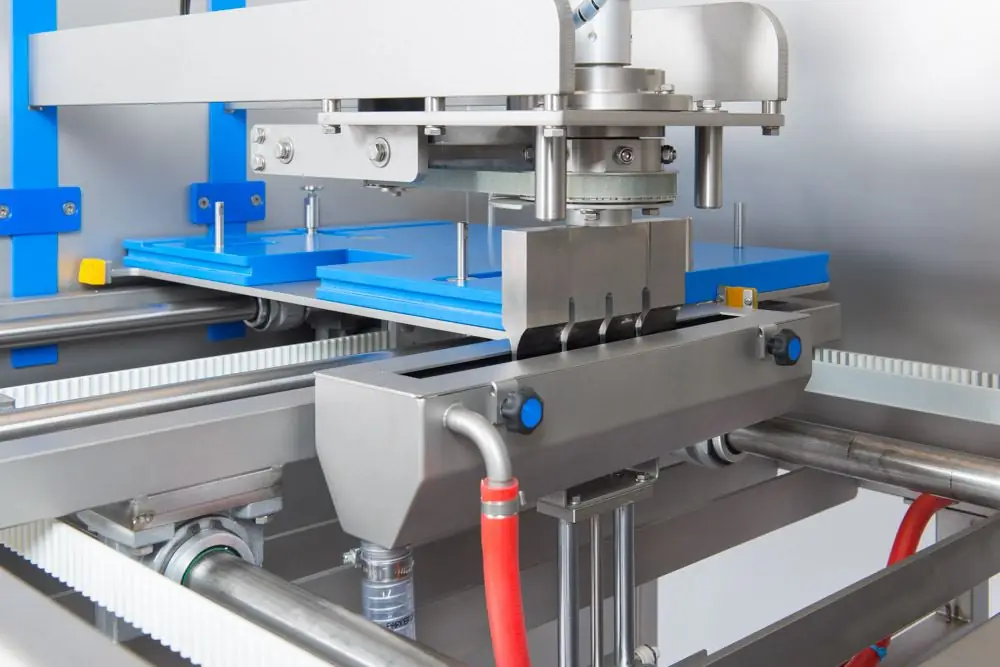
Kovozpracující průmysl je v této fázi vývoje schopen řešit složité úkoly řezání a vrtání obrobků různého stupně tvrdosti. To bylo možné díky vývoji zásadně nových způsobů ovlivňování materiálu, včetně široké skupiny elektromechanických metod. Jednou z nejúčinnějších technologií tohoto typu je úprava ultrazvukem (UZO), založená na principech elektroakustického záření
Odlévání do silikonové formy: zařízení. Vakuové lití do silikonových forem
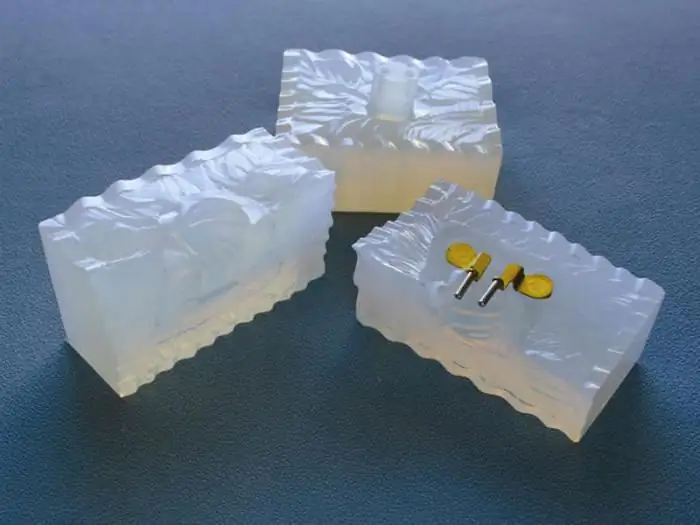
Pro výrobu malého počtu plastových polotovarů se nejčastěji používá vakuové lití do silikonových forem. Tato metoda je poměrně ekonomická (výroba kovové formy vyžaduje více času a peněz). Silikonové formy se navíc používají opakovaně a to také výrazně zlevňuje výrobu
Výhody a nevýhody polyesteru: popis materiálu, výhody použití, recenze
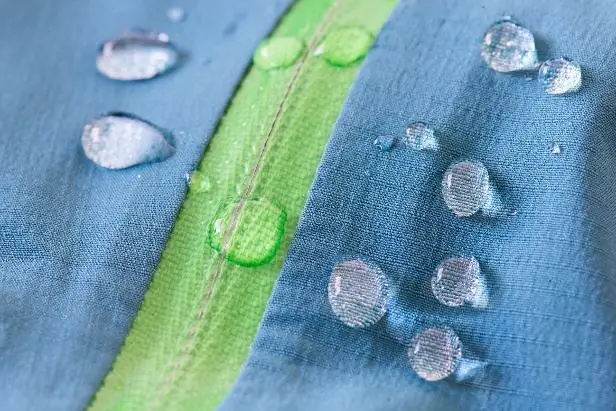
Polyester lze nalézt ve složení téměř každého předmětu, který je přítomen v šatníku každého člověka. Vyrábí se z něj nejen oblečení, ale i boty, deky, termoprádlo, koberce. Jaké jsou vlastnosti jednotlivých typů polyesterových výrobků. Výhody a nevýhody těchto produktů jsou popsány v našem článku